RBA Annual Conference – 1994 Internationalisation, Firm Conduct and Productivity Henry Ergas and Mark Wright[*]
1. Background and Overview
For much of the post-war period, Australia's economy was relatively insulated from international trade. In part, insulation reflected the costs arising from distance. However, the high levels of assistance provided to import-competing manufacturing during, and after World War II, also played an important role. Taken as a share of GDP, gross trade declined from the relatively high levels it had earlier achieved (Figure 1). By the 1960s, when trade levels in the other industrial countries were booming, Australia's trade share seemed unreasonably low (Kuznets 1959). Sheltered behind protective walls, manufacturing expanded rapidly (Figure 2), with an industrial structure characterised by high levels of concentration, as a small number of firms shared the relatively small domestic market. Each of these firms (the larger ones frequently being foreign owned) produced too broad a range of products, using plants too small to ever achieve economies of scale, making what were intended to be promising ‘infant industries’ into premature geriatrics. Market disciplines being weak, managerial slack was pervasive, as was the sharing of rents through the system of centralised wage determination. All of this contributed to the slow rate of productivity growth identified as a central concern by the Vernon Committee and by the first OECD survey of Australia.
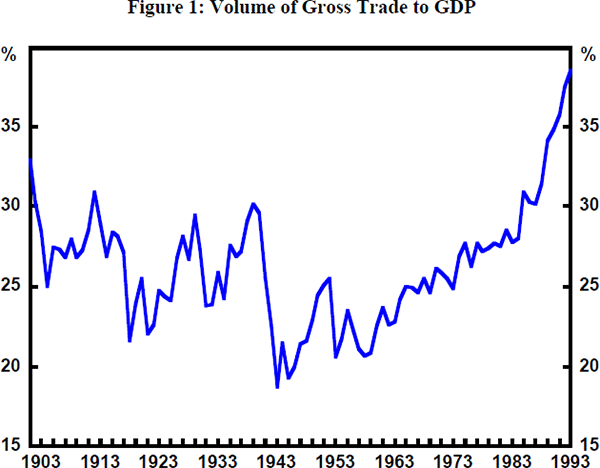
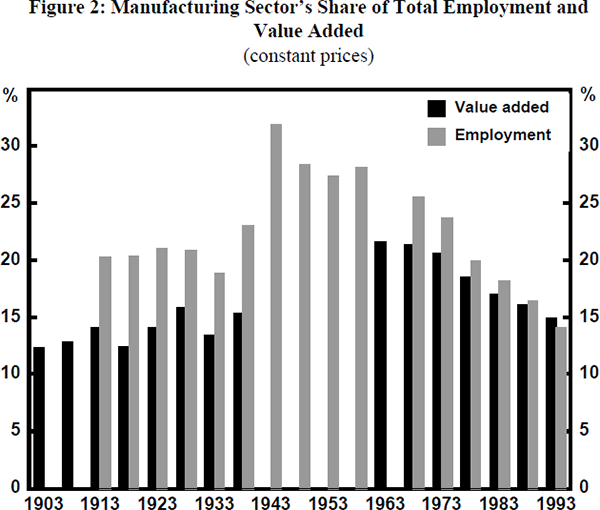
By the early 1990s this characterisation seemed increasingly out of date, if not completely dated. Gross trade as a percentage of GDP (both expressed in real terms) rose from just under 25 per cent in 1972/73 to around 39 per cent in 1992/93. This increase paralleled substantial reductions in protection, with the effective rate of assistance to manufacturing reduced by two-thirds (from 35 per cent in 1972/73 to around 12 per cent 20 years later). The former adviser to the Hawke Government, Ross Garnaut, has written that the transformation was ‘bigger than the end of the British Corn Laws that earned Peel and Cobden a dozen pages in our high school history books, eight or ten time zones and over a century away’ (Garnaut 1991). And though this statement contains an element of exaggeration, the extent of the reforms remains startling in historical perspective.[1]
Underpinning the change was the government's conviction that ‘suppliers of goods and services which are protected from international competition […] are not subject to the pressures which ensure efficient management and production’ (One Nation 1992). And undoubtedly, the changes must have had substantial impacts on the ways in which manufacturing firms work and the efficiency with which they use resources. Ultimately these changes should allow sustainable increases in living standards.
However, to date there is little evidence of a significant increase in the trend rate of productivity growth. Figure 3 presents data on labour productivity in the non-farm sector for the period from 1978/79 to 1993/94. The mid 1980s productivity slowdown was probably influenced by the extended period of wage moderation, which reduced capital-labour substitution. However, the path which succeeded it cannot, at this stage, be said to be above that of the past.
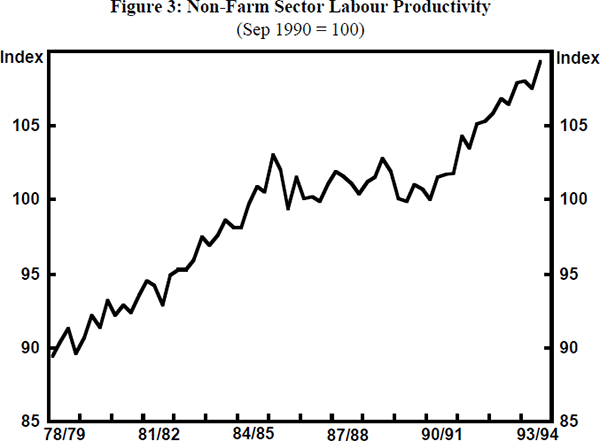
That it should be difficult to detect unambiguous traces of the influence of structural change on productivity growth is not surprising, for at least three reasons. First, short-run productivity trends reflect the interaction of a large number of cyclical and structural forces that cannot readily be disentangled.[2] Second, even in looking at the longer run, when the instruments of growth accounting can be deployed, economists have rarely been able to satisfactorily explain more than half of the observed change in output.[3] Finally, it is reasonable to hypothesise that the economy is still in the adjustment process, with changes occurring that will only really show up in the aggregates sometime down the road.
Given these difficulties it is important to examine the changes underway at a micro-level – that is, to assess the extent to which, and the ways in which, adjustment is proceeding both within, and between, industries. This is the primary task of this paper. To do this, we draw on a new data source, namely a survey of Australian manufacturers carried out by the Australian Bureau of Statistics (ABS) on behalf of the Australian Manufacturing Council (AMC).
The analysis in the paper addresses three specific questions:
- How far has the process of international integration gone? Is Australia now integrated into the world economy to an extent comparable to that of other small, industrial countries?
- How has integration affected the pattern of resource allocation between industries, notably within manufacturing? To what degree has Australian manufacturing become more specialised?
- Within industries, to what extent, and through what channels, has economic integration affected productive efficiency?
The paper's main findings can be summarised as follows. First, though the trade intensity of the Australian economy is still below the average for the industrial economies, the gap has diminished in recent years and, the extent to which it persists, largely reflects Australia's distance from major markets (Section 2).
Second, rapid internationalisation has been associated with greater specialisation in trade and output within manufacturing, and with accelerated structural change in the pattern of employment (Section 3).
Third, though the data do not allow us to examine changes in the behaviour of individual enterprises over time, there is strong cross-sectional evidence of international exposure affecting behaviour and performance within industries. These effects work partly through intensified competition, which typically leads to increased product quality and reduces intra-industry disparities in performance. But the main impacts come from involvement with foreign markets, as it is outward orientation, rather than market circumstances, which is most strongly associated with superior performance (Section 4).
In terms of the links between international exposure and firm performance we hypothesise three major effects: international exposure will encourage greater learning, as firms come into contact with, and measure themselves against, a broader range of rivals; it will force managers to tackle inherited inefficiencies; and it will encourage greater selection (as weaker firms are forced to adjust or decline). The results in Section 4 provide some support for these hypotheses and suggest the following:
- Involvement in the international economy provides firms with expanded opportunities to learn. Firms more heavily involved with the international economy (be it through exporting or through foreign direct investment) are more likely than are domestically-oriented firms to: systematically measure themselves up against world-best practice; focus on improving product quality and customer satisfaction; and successfully learn from customers and suppliers. All of these activities feed into productivity gains in the medium term.
- International involvement is also associated with greater efforts to tackle many of the rigidities which have long characterised the Australian economy. Though internationally-oriented firms are most likely to regard the current industrial relations arrangements as constraining, they also report greater success in implementing enterprise agreements that work, and are more likely to regard unions as playing a positive role in their plants.
- These differences in characteristics are associated with substantial differentiation within industries. The factors which most sharply distinguish the better performing firms are investment in intangible assets (mainly skills and R&D), less conflictual industrial relations, and a more systematic emphasis on monitoring their performance relative to rivals. Importantly, there remains a very substantial tail of firms – accounting for nearly 20 per cent of manufacturing employment – which does not export, carries out little or no R&D, and seems to make no investment in monitoring its competitive position. Nearly half of these firms supply intermediate inputs, so that their performance could act as a substantial constraint on the competitiveness of their clients. The disparities in performance tend to be greatest within industries with above average concentration and benefiting from high levels of assistance. Moreover, we find evidence of growing differentiation and specialisation within industries, as competition sorts out the good performers from those which lag.
Finally, some of the policy implications of these results are explored in Section 5.
2. Australia's Internationalisation in Comparative Perspective
The extent to which countries are integrated into the world economy depends partly on policy variables – such as the extent of protection – and partly on structural variables, such as size and distance from major markets. Since the pioneering work of Hirschman (1945), Maizels (1963) and Kuznets (1959), a substantial body of literature has developed on the way each of these variables contributes to shaping patterns of openness and trade. Drawing on the hypotheses developed in this literature, it is possible to examine empirically whether in the past, Australia was less integrated with the world economy than might have been expected on the basis of the structural variables alone; and equally, to assess the extent to which any such gap may have diminished in recent years. Subsequent sections carry out this analysis first for international trade and then for international investment.
2.1 International Trade
The ratio of gross trade (imports plus exports) to GDP is conventionally used as a measure of openness to international trade, though it is perhaps better (and more neutrally) described a measure of trade intensity.[4] Following Kuznets and Hirschman, it seems reasonable to suppose that four factors will affect the value this measure takes for a particular country. These are:
- A rise in per capita GDP will, on balance, tend to increase trade intensity as it is generally associated with greater demand for diversity. So long as product differentiation entails fixed costs, an increase in per capita GDP, holding everything else constant, will involve a higher level of imports and hence of exports.
- Higher GDP, on the other hand, will tend to be associated with reduced trade intensity, since at a given level of GDP per capita, larger economies will be able to satisfy a higher share of their needs through internal sources, thereby reducing transport costs.
- Greater proximity to potential markets increases trade intensity by reducing the natural protection which comes from the cost of transport and communications, and by diminishing the cultural distance separating market participants.
- Finally, higher trade barriers will reduce trade intensity by discouraging imports and taxing exports.
Table 1 sets out the results of a regression incorporating these variables, together with a dummy variable for Australia. The model has been estimated for 1975, 1980, 1985 and 1990 over a panel of 56 countries accounting for the vast bulk of world income. While a more detailed discussion of sources and methods is provided in Appendix A, it is clear from the table that – with the exception of the (generally insignificant) protection variables for the industrial economies – all the coefficients on the Hirschman-Kuznets variables have the expected sign and are strongly significant. These results, together with those in Table 2, suggest the following:
1975 | 1980 | 1985 | 1990 | |
---|---|---|---|---|
Australian dummy | −0.148 (0.304) |
−0.108 (0.293) |
−0.050 (0.263) |
0.068 (0.291) |
Real GDP | −0.220** (0.021) |
−0.220** (0.021) |
−0.220** (0.021) |
−0.220** (0.021) |
Real GDP per capita | 0.234** (0.065) |
0.234** (0.065) |
0.234** (0.065) |
0.234** (0.065) |
Proximity to world production | 0.002** (0.001) |
0.002** (0.001) |
0.002** (0.000) |
0.002** (0.000) |
Protection × (D1+D2) | −0.001 (0.010) |
−0.013 (0.076) |
−0.025 (0.106) |
0.041 (0.247) |
Protection × (D3) | −0.493 (0.329) |
−0.593** (0.201) |
−0.557* (0.247) |
0.078 (0.388) |
Protection × (D4) | −0.664** (0.228) |
−0.441** (0.153) |
−0.406** (0.138) |
−0.323* (0.130) |
D1 {Industrial Countries} | 1.983** (0.628) |
2.115** (0.625) |
2.033** (0.617) |
1.809** (0.630) |
D2 {Western Hemisphere} | 1.941** (0.537) |
1.975** (0.540) |
1.848** (0.526) |
1.812** (0.532) |
D3 {Africa, Middle East, Other Europe} | 2.302** (0.548) |
2.412** (0.548) |
2.282** (0.551) |
1.946** (0.576) |
D4 {Asia} | 2.751** (0.521) |
2.863** (0.521) |
2.646** (0.524) |
2.682** (0.540) |
![]() |
0.68 | 0.70 | 0.75 | 0.68 |
Notes: (a) Trade intensity is equal to ![]() (b) Real GDP and real GDP per capita are in logs. (c) Standard errors are in parentheses. (d) * (**) denote coefficients which are significant at the 5% (1%) significance level. (e) The protection variable is represented by three variables which allows for slope variation. (f) The test statistic for the restrictions that the coefficients on real GDP and real GDP per capita are equal across time is Χ2 (6) = 4.212. The null hypothesis cannot be rejected at the 1% significance level. These restrictions have been imposed. |
1960 | 1965 | 1970 | 1975 | 1980 | 1985 | 1990 | |
---|---|---|---|---|---|---|---|
Australia | 31.5 | 31.3 | 28.9 | 28.8 | 33.9 | 35.3 | 34.5 |
United States | 9.4 | 9.4 | 11.3 | 16.1 | 20.8 | 17.1 | 21.1 |
Canada | 36.0 | 38.4 | 42.9 | 47.2 | 55.1 | 54.5 | 50.5 |
Germany | 35.3 | 35.6 | 40.3 | 46.5 | 53.3 | 61.5 | 58.4 |
France | 26.9 | 25.8 | 31.1 | 36.9 | 44.3 | 47.2 | 45.3 |
OECD(b) | 47.6 | 47.5 | 52.4 | 56.2 | 63.9 | 68.5 | 63.8 |
World | 45.3 | 44.8 | 47.6 | 55.7 | 61.1 | 60.0 | 61.0 |
Notes: (a) The trade intensity ratio is defined as the sum of exports and
imports as a proportion of GDP (all in current prices). Source: Penn World Table (Mark 5.5), ‘OPEN’ variable. |
- Australia's trade intensity is well below the average for the OECD and the world as a whole, and has been so for the entire period covered in Table 2.[5] The gap opened up in the late 1960s, as the trade intensity of the Australian economy actually fell, whilst for most other countries it continued to rise. More recently, Australia's trade intensity has risen, whilst that of the OECD and the larger group of countries appears to have plateaued.
- The rise in Australia's trade intensity between 1975 and 1990, although partly explained by the structural determinants of trade intensity, can be mainly attributed to a decline in the degree to which Australia is peculiar. Although imprecisely estimated, the Australia dummy was negative, large and economically significant in 1975. By 1990, this was no longer the case.
- The remaining gap between Australian and average OECD trade intensity is still substantial in absolute terms, being equivalent to almost 30 per cent of 1990 GDP. However, it is largely attributable to the variable capturing proximity to world production. If Australia was located as close to the centre of world production as France, the estimates suggest that its trade intensity in 1990 would be more than twice as large, at 73 per cent of GDP.
- Though the Asian countries tend to trade especially heavily, as is apparent from the intercept dummy for Asia, their trade intensities are also significantly influenced by trade protection. While the coefficient on the protection variable has been diminishing over time, its continuing weight highlights the gains in terms of expanded world trade, and presumably incomes, that could accrue from further liberalisation in the region.
2.2 Foreign Direct Investment
Increases in trade intensity have been paralleled by a continued rise in foreign direct investment (FDI). Substantial difficulties are involved in comparisons of FDI between countries and over time. These difficulties arise because of differences in the treatment of retained earnings, in the valuation bases used, in the treatment of debt and in the control thresholds used for defining foreign ownership. As a result, the international data, and notably the series collected by the IMF and the OECD, are not fully comparable. They can, nonetheless, be suggestive of broad trends and it is in this spirit that they are examined here.
Expressed in current prices, cumulated FDI inflows to Australia were some five times greater during the period 1981–1992 than during 1973–1980 (a period of unusually low FDI inflows).[6] Comparing these two sets of years, Australia's share of OECD inward direct investment – that is, the ratio of FDI inflows to Australia, to all FDI inflows to countries in the OECD area – remained roughly constant at around 5 per cent, but out of a strongly rising total.
At the same time, there has been a shift in the sectoral allocation of FDI away from manufacturing, mining and agriculture towards the service industries. In particular, manufacturing's share of cumulated FDI fell from 35 per cent in 1976–81 to 27 per cent in 1982–92. This may partly reflect the impact of reductions in assistance on the incentive to ‘leap over the tariff wall’ which earlier studies found to be an important component of FDI into Australia. It is also no doubt related to the falling significance of manufacturing in the economy as a whole. Nevertheless, foreign-owned firms still account for a large proportion of activity in the manufacturing sector. The latest ABS figures, which refer only to 1986/87, show that the share of foreign-owned firms in manufacturing value added has remained fairly stable at around 31 per cent since the mid 1970s.[7]
In contrast to the mixed picture for the inward flows, Australia's share of OECD outflows of FDI – that is, its importance as a home country for FDI – increased markedly during the time period considered. Taking the period 1973–1980, Australia accounted for less than 1 per cent of cumulated outflows of FDI from OECD countries. This more than doubled to just under 2 per cent for the period 1981–1992. Australia's FDI outflows in this latter period exceeded those of Canada and Switzerland, traditionally substantially larger foreign investors than Australia, and were barely smaller than those of Sweden.
The extent and pattern of the increase in Australian FDI can be examined using US Department of Commerce data on FDI inflows into the United States. While Australian firms accounted for barely 0.5 per cent of annual inflows of FDI into the United States in 1980 (and even less before then), their share quadrupled to between 2 and 2.5 per cent for 1985, 1986, 1987 and 1988 and then seemed to stabilise at around 1.5 per cent in 1990 and 1991. As with foreign trade, this substantial rise points to the shrinking, and perhaps even disappearance of a gap between the actual level of Australian FDI and that which might be expected from an economy with Australia's characteristics.
Much as with trade intensity, this hypothesis can be analysed by considering the factors that are likely to influence a country's share in FDI inflows into a particular host market. Drawing on the Dunning-Caves ‘eclectic’ model of foreign investment, it can be hypothesised that this share will be associated with: the size of the home country's economy; its distance from the market in question; the home country's level of technological and managerial sophistication as reflected in per capita income and in its share of cumulated OECD area R&D expenditures; as well as an exchange rate variable capturing the familiar Aliber effects.
A regression model estimated on this basis (with county shares of FDI inflow into the US over the period 1976–1992 as the dependent variable) explained some 36 per cent of the variance in the data, though all the coefficients were statistically significant at the one per cent level. The results of this model suggest that the Australian share was significantly below the expected level in the period to the mid 1980s, and significantly above it from then on.[8]
2.3 Summary
Three major results can be drawn from the data presented above.
First, though the trade intensity of the Australian economy remains below that of other OECD countries, the gap has fallen substantially in recent years, and could fall further as a result of income growth in Australia's region, reductions in transport and communications costs, and cuts in protection in the Asian economies. Second, Australia remains relatively open to foreign direct investment, and has attracted continuing substantial inflows of FDI despite reduced incentives for simple import substitution. Third, Australian outflows of FDI increased very markedly over the course of the 1980s – indeed, to a point where (at least on the basis of US data) they exceeded the levels which might have been expected given Australia's economic size and structure. Combined, these results highlight the continued rapid internationalisation of Australia's economy.
3. Output and Resource Shifts Between Industries
The closer integration of the Australian economy into world markets can be expected to affect efficiency by altering the allocation of resources between industries, and by changing conduct and performance within industries. The former corresponds to the familiar mechanisms of Ricardian comparative advantage; the latter, though it has long been referred to in studies of international trade and investment, has only very recently been given a firmer analytical basis. These two, by no means mutually exclusive, types of effects are considered respectively in this section and in the next.
The factors and processes underlying changes in the pattern of output and resource use are well known. They centre on the changes in relative product prices associated with increased international integration, which should alter the structure of the economy and shift resources between industries. In principle, since protection has been reduced rather than removed, the effects on welfare are difficult to gauge a priori. Nonetheless, it seems reasonable to assume that reductions in assistance of the magnitude observed should be welfare increasing, as the shifts in resources in line with comparative advantage result in the transfer of resources from less to more valued uses, raise productivity measured at world prices and increase national income (see Dowrick in this Volume).
The data available do point to inter-industry shifts within manufacturing. By and large, these shifts have resulted in greater specialisation, both in terms of output and trade.
Output specialisation can be examined by assessing trends in the sectoral distribution of value added, and by measuring the degree to which a few industries dominate manufacturing net output. As a result of natural and policy protection, the Australian manufacturing sector has traditionally been far less specialised than its counterparts in other small industrial economies, most strikingly those in Europe. However, the gap in this respect between Australia and comparable countries overseas has diminished somewhat in recent years.
The relevant data are set out in Figure 4. The OECD's STAN database, which provides value-added data for 26 industry groups, has been used to calculate a Herfindahl index of manufacturing industry value added, with higher values of the index implying a higher degree of specialisation. The data cover the period from 1970 to 1989 (observations for some countries are available up to 1991). Increases in the value of the index for Australia occurred in the early 1970s, in the late 1970s and then in the period from 1985. At the end of the 1980s, the value of the index for Australia was similar to that for Canada, but was still well below that for the small open European economies.
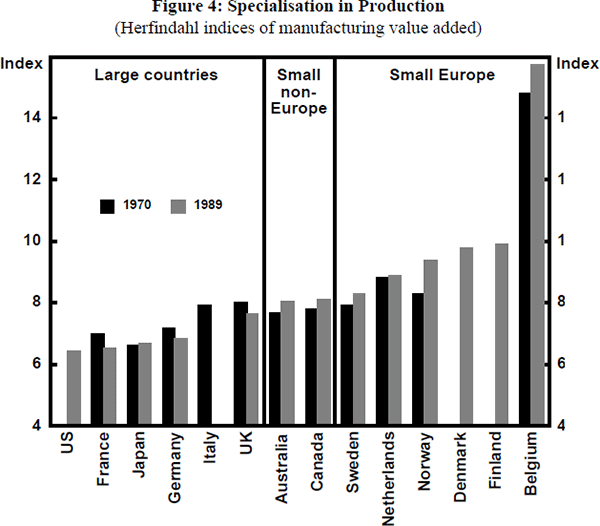
These is also some evidence of increasing specialisation in international trade. Two indicators have been examined in this respect.
The first uses series on trade and output corrected for the double counting of own-industry intermediate inputs. (These series are described in Appendix B.) These data are used to calculate ratios of import penetration, and export orientation, in volume terms for the 12 ASIC 2-digit manufacturing industries. The results, set out in Figure 5, point to increased inter-industry dispersion, in the sense that the standard deviation of the measures rise over time. However, because the means for both series increased even more rapidly, the unweighted coefficients of variation have actually tended to decline.
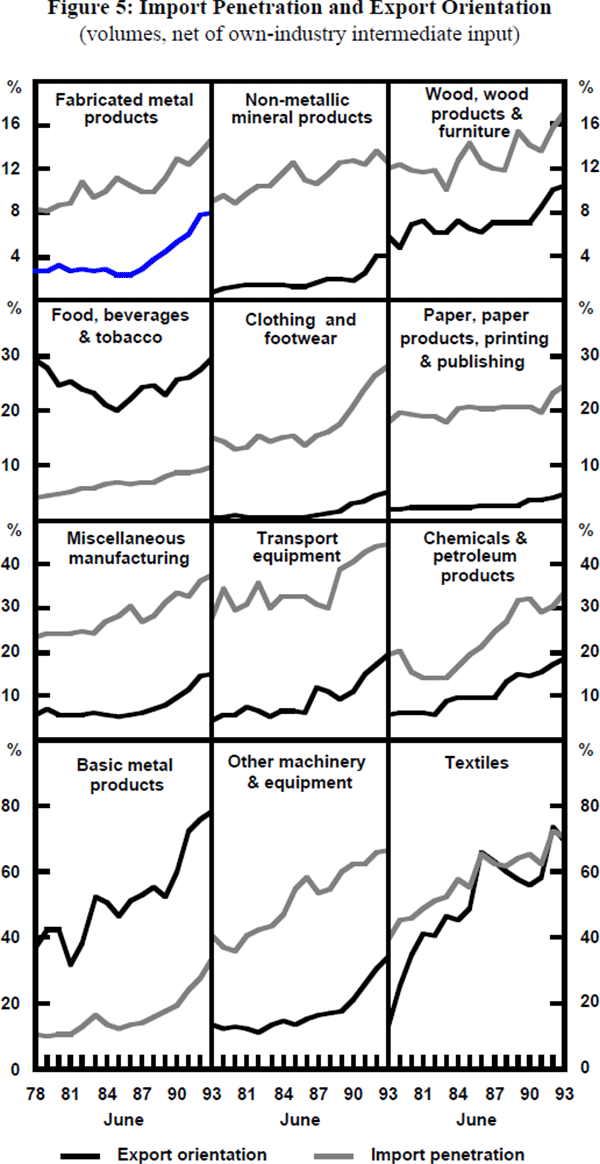
The second indicator of trade specialisation examined is the Balassa index of revealed comparative advantage (RCA).[9] The data are drawn from the STAN database and use trade data reclassified to the 26 STAN manufacturing industry groups. Table 3 sets out the summary statistics for the RCA estimates for 13 OECD countries, including Australia, for 1979 and 1990 (the last year for which data are available).
Median | Mean | Variance | Skewness | Kurtosis | ||||||
---|---|---|---|---|---|---|---|---|---|---|
1979 | 1990 | 1979 | 1990 | 1979 | 1990 | 1979 | 1990 | 1979 | 1990 | |
Australia | 0.38 | 0.50 | 1.56 | 1.68 | 12.49 | 12.98 | 2.84 | 3.31 | 9.27 | 13.20 |
Canada | 0.61 | 0.63 | 1.53 | 1.38 | 5.29 | 3.37 | 2.48 | 2.21 | 8.61 | 7.13 |
Denmark | 0.83 | 0.88 | 1.24 | 1.36 | 2.66 | 2.33 | 3.20 | 1.95 | 13.40 | 5.78 |
Finland | 0.55 | 0.73 | 1.89 | 1.75 | 18.50 | 12.66 | 3.60 | 3.71 | 15.42 | 16.10 |
France | 0.98 | 0.90 | 1.22 | 1.18 | 0.80 | 0.50 | 2.30 | 0.87 | 8.73 | 2.55 |
Germany | 0.99 | 0.94 | 1.06 | 1.03 | 0.33 | 0.26 | 0.36 | 0.32 | 1.99 | 1.77 |
Italy | 1.06 | 1.06 | 0.99 | 0.98 | 0.10 | 0.04 | −0.81 | −1.07 | 2.57 | 3.11 |
Japan | 0.85 | 0.67 | 1.02 | 1.05 | 0.69 | 0.96 | 0.81 | 1.06 | 2.55 | 3.06 |
Netherlands | 0.72 | 0.79 | 1.18 | 1.26 | 1.21 | 1.36 | 1.45 | 1.59 | 4.60 | 4.64 |
Norway | 0.52 | 0.57 | 1.96 | 2.34 | 13.25 | 17.76 | 2.63 | 2.40 | 9.00 | 7.34 |
Sweden | 0.97 | 0.93 | 1.41 | 1.37 | 4.26 | 2.73 | 3.51 | 3.35 | 15.23 | 14.42 |
UK | 0.87 | 1.02 | 1.49 | 1.31 | 2.50 | 1.01 | 2.98 | 1.40 | 12.32 | 5.06 |
US | 0.92 | 0.89 | 1.61 | 1.30 | 6.74 | 1.66 | 3.78 | 2.56 | 16.17 | 10.44 |
Note: Calculated as shown in footnote 9. |
In both years, the median RCA for Australia has been the lowest among the countries considered. Given the way the index is normalised, this points to a relatively skewed pattern of trade. This is borne out by the values of the indicators of skewness (third moment) and kurtosis (fourth moment). A major factor here are the very high RCAs for manufactures that are not elaborately transformed, notably Non-Metallic Minerals and Food, Beverages and Tobacco. Only Finland, with its concentration on exports of pulp and paper, has a similar pattern.
The degrees of skewness and of kurtosis have also tended to rise over time. Sharp increases during the 1980s in the RCA index for Non-Metallic Minerals appear to have been a major contributor to this change. A regression analysis of the RCAs on time shows that RCAs have also increased significantly for Petroleum Products, Textiles and (though to a lesser extent) Iron and Steel, and have declined significantly for Food, Beverages and Tobacco, Chemicals (excluding drugs) and Metal Products, while remaining stable, or displaying no clear trend, for the other industry groups.
Specialisation in trade and output have been accompanied by shifts in the pattern of resource use. Figure 6 sets out Lawrence indices of structural change calculated annually over the period from 1975 to 1994.[10] The results are presented first for manufacturing, and then for the entire non-farm economy (but keeping the 13 manufacturing subdivisions separate). Though this measure can be distorted by oscillations in industry shares, a broadly similar picture emerges when rolling 5-year-ended data are used. The results point to an increase in the year-on-year rate of structural change in manufacturing, with an especially marked rise in the extent of the shifts in employment.
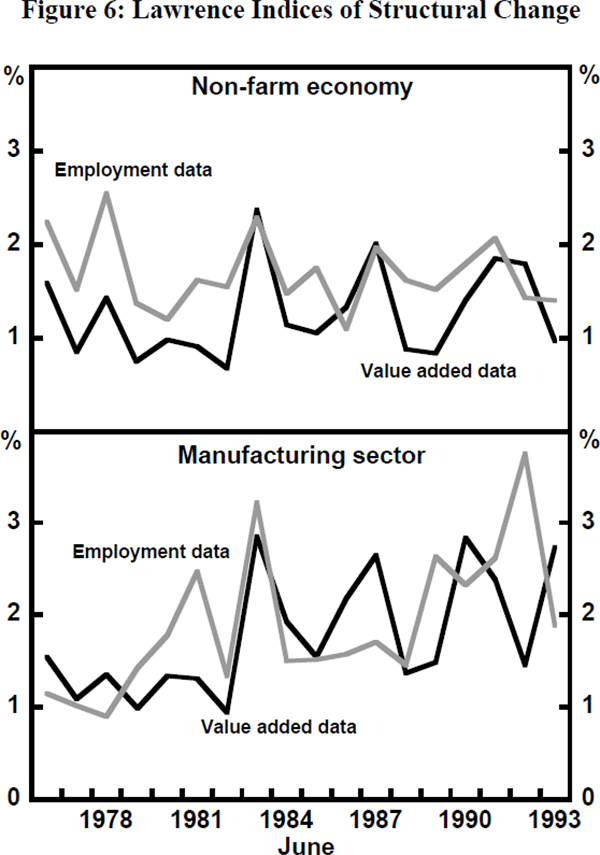
However, at least on a preliminary analysis, it is not apparent that these shifts are any larger than those experienced in other small industrial economies, as the need to reverse the legacy of a long period of protection might have suggested. For example, an indicator of structural change derived from the OECD's ISDB database[11] suggests a significantly greater stability of industry shares in Australian manufacturing employment than observed in Canada, Sweden or the UK.[12] A similar picture emerges from the ISDB data on capital stocks, though greater doubts must be expressed about the reliability of these estimates.
Moreover, we find no relationship between the pattern of output change and the extent, or direction of changes, in revealed comparative advantage. Going by the data on Australian manufacturing in STAN for the period 1970–89, there was a statistically significant association between changes in RCAs and changes in output shares for only 3 of the 22 industry groups.
This suggests some caution about the extent and pattern of inter-industry shifts in resource use. Three factors may be at work.
First, protection remains significant for some of the industry groups which, were they fully exposed to international competition, might experience the largest shrinkages. This is notably the case for passenger motor vehicles and for textiles, clothing and footwear (TCF) – and indeed, the ISDB data indicate that Australia has experienced smaller declines in employment in TCF over the past two decades than most other OECD economies (Figure 7).

Second, change in the composition of employment may have been slowed by the extended period of wage restraint in the 1980s. Much as appears to have happened in the United States, low rates of wages growth may have offset the adjustment pressures which economic integration would otherwise have placed on low-productivity sectors.
Third, even in those sectors where adjustment is now underway, the transition period may extend well into the future. The current slow rate of change is not necessarily a reliable indicator of longer-term outcomes.
In short, further shifts in the pattern of resource use within manufacturing may still lie ahead. However, it would be wrong to think that these shifts are inevitable. After all, predictions of pure specialisation in line with comparative advantage and determined by factor proportions can only be derived on the basis of strong simplifying assumptions. It is increasingly recognised that, under conditions of imperfect competition, the patterns of specialisation which emerge from free trade may bear little resemblance to those expected from Ricardian models of comparative advantage. Indeed, in recent work which extends the general equilibrium (GE) model to include oligopoly, and then derives GE models of trade under imperfect competition, the equilibrium pattern of output is largely indeterminate (Gabszewicz and Michel 1992; Cordella 1993). In these models, most of the effects of integration arise from changes in behaviour within industries – a result not inconsistent with the long-term trends characterising the advanced economies.
Some indication of the relative importance of inter as compared with intra-industry shifts can be obtained by comparing the contributions to manufacturing labour-productivity growth of changes within industries on the one hand, (the upper panel in Figure 8) and of shifts in the allocation of labour between industries on the other (the lower panel in the same figure).[13] In virtually all instances, the first dominates the outcome; this suggests that it is within industries, rather than in intersectoral reallocation, that the greatest effects of international integration will be found.
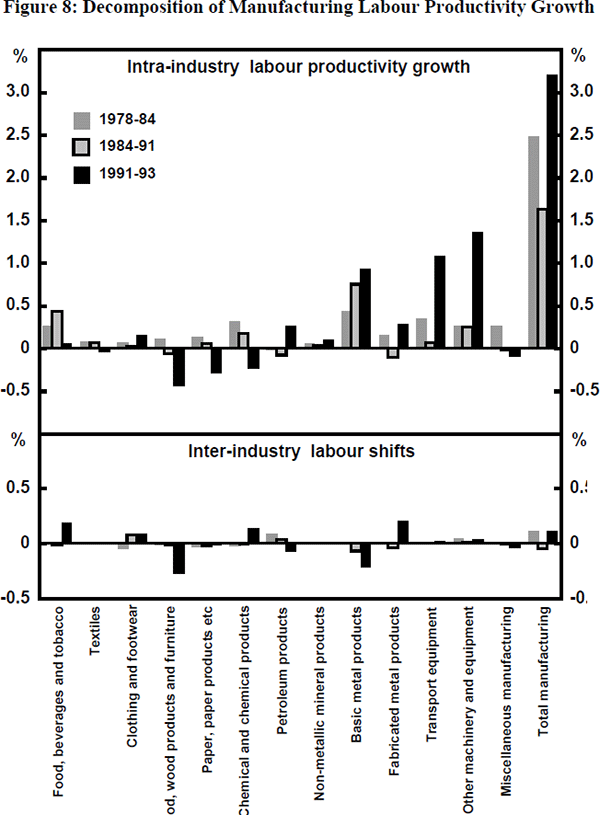
4. Changes in Performance Within Industries
If the major benefits of trade reform are concentrated within industries, we would hope to find some evidence of the link between the international environment and firm behaviour using firm-level data. To this end, this section begins by examining the analytical reasons for expecting such a relationship; then draws on these reasons to develop testable hypotheses; and finally sets these hypotheses against data drawn mainly from the AMC survey.
4.1 The Analytical Background
Increased international integration is likely to affect efficiency at the level of the firm and the industry primarily through its impact on the intensity of competition. By reducing price-cost margins, notably in concentrated industries, greater competition will yield improvements in allocative efficiency; but it may also increase technical efficiency – that is, the productivity with which resources are used. It is the latter which is the prime concern of this paper and recent, largely theoretical work identifies three mechanisms through which it may be affected by changing product market conditions.
4.1.1 Yardstick efficiency
The first of these is the impact of product market conditions on agency costs – that is, on the costs owners face in ensuring that managers have adequate incentives to maximise shareholder value. The underlying notion is that in a more competitive market, owners can more readily compare the performance of the firms in which they have invested, to the performance of other firms. This allows them to discriminate between say, low profits due to industry-wide demand shocks and low profits due to managerial slack or to rent-sharing between managers and workers. As a result, owners can better structure the incentives managers face, securing a closer alignment between managerial actions and shareholder objectives. This will reduce managerial slack, and ensure that prior inefficiencies are wound back.
Two points are worth noting. The first is that greater monitoring by owners of the comparative performance of managers can be expected to lead the managers themselves to invest more heavily in comparing their performance with that of managers in other firms. Second, just as competition increases the ability of owners to monitor their agents, it makes it easier for managers to monitor the performance of the firm's other employees. As a result, intensified competition should be reflected in the tighter assessment of performance at all levels of organisation.
4.1.2 Sampling efficiency
Though yardstick efficiency depends on the basic factors determining profits within a firm being highly correlated across firms[14] (since this is what allows managerial performance to be compared), product market competition may also yield efficiencies when the firms within an industry differ in important respects. In particular, if firms are viewed as ‘taking bets’ on particular ways of doing things, having a greater number of firms in a market will, all other things being equal, accelerate the rate at which the most efficient approaches are discovered. To the extent that there are spillover effects (that is, the firms in an industry can learn from each other, for example through the yardstick effects of benchmarking), experimentation will increase efficiency, not only in the innovating firm, but also across the firm population as a whole.
Greater international exposure can be a particularly effective means of enhancing this process of ‘letting a thousand flowers bloom’. It provides for a vast increase in the number of sampling points, as domestic firms are exposed to the example of firms overseas. Inward investment by foreign firms can also be used to ‘show-case’ technologies, organisational approaches and marketing techniques not in widespread use in the domestic market (though it can also have the effect of accentuating the barriers to entry confronting domestic entrepreneurs). In addition, through exporting to, and investing in, foreign markets, domestic firms may become more aware of foreign sources of technology. Finally, and perhaps especially significantly, gains may come from access to a broader range of intermediate inputs and capital goods. In addition to its immediate cost-reduction impact, the expansion in goods available, effectively lowers the costs of innovation. This effect will extend to the non-traded sector as well, which thereby benefits directly from increased integration into the world economy.[15]
4.1.3 Selection efficiency
In addition to effects at the level of the firm, increased product-market competition will alter the process by which inefficient firms are ‘weeded out’ and efficient firms are rewarded. The presumption here is that firms are indeed asymmetric, and that superior performance cannot be costlessly imitated. Stronger product-market competition is then presumed to result in the more rapid and complete sorting of firms into distinct performance classes, with the less productive firms being forced to exit the market. The most natural route through which this Darwinian process occurs is the reduction in price-cost margins brought by increased competition, since this will make it more difficult for inefficient firms to survive.[16] At the same time, owners, now better able to compare performance, are not likely to continue funding inefficient firms, while potential employees, mindful of the costs of redundancy, may become more wary of accepting jobs in the firms least likely to survive. As a result, inefficient firms will face tighter price and cost constraints, making their continued existence less likely.
4.1.4 Caveats
While each of these factors suggests that intensified product-market competition will be associated with increased technical efficiency, a number of caveats are worth noting.
First, the dynamics of adjusting to greater competition may be complex and costly. In particular, firms that are faced with the likelihood of exit may have strong incentives to curtail investment and raise prices, especially when their more efficient rivals realise that this is merely a transitory end-game strategy. Under these circumstances, it can be a profit-maximising strategy for the likely survivor to slow their own expansion (as they wait for exit to occur), so that the overall price level for the industry actually rises. The prediction that industry efficiency will be enhanced may then be realised only very slowly.
Second, even putting the adjustment dynamics aside, the precise features of the ‘equilibrium’ towards which the system is heading are not necessarily as straightforward as the above discussion suggests. This is especially so when firms can choose to compete through sunk investments such as outlays on advertising, R&D, or the holding of inventories and other forms of excess capacity. In these cases, in which sunk costs are endogenous, the expected outcomes depend very heavily on the precise characterisation of the competitive process. For example, where competition occurs largely through advertising, an increase in the threat of competition (due say, to an expansion of the market) may lead to a rise in costs, as incumbents increase outlays so as to protect their market position.
Equally, where fixed costs are large and sunk (for example, because production requires capital goods that have few alternative uses and a finite and relatively predictable lifetime), reduced barriers to new competition are not necessarily associated with greater productive efficiency, since they may result in excess entry and over-capacity. Last, but by no means least, is the Schumpeterian conjecture, according to which some degree of allocative inefficiency – that can only be sustainable if competition in the market is imperfect – is needed if firms are to make the investments required to compete for the market.[17]
In each of these cases, the prediction that greater competition will increase productive efficiency may not hold true, at least over some possibly significant range of the intensity of competition scale.
4.2 Implementation and Hypothesis Formulation
While the mechanisms reviewed above cannot easily be set against empirical evidence, they can be used to develop testable hypotheses. These hypotheses fall into three broad groups.
4.2.1 Integration, learning and performance
A first set of hypotheses relates integration, learning and performance.
Agency cost models of the firm, briefly described above, provide a starting point. In these models, intensified competition increases the incentives and capabilities of owners to strike efficient contracts with managers. Significant here is the ability of owners to make a broader range of comparisons between firms, and hence more readily distinguish good from poor managerial performance.[18] Given this link, it would seem reasonable to expect that managers, faced with an expanded set of competitor firms, will themselves have increased incentives to systematically monitor the behaviour of rivals and compare corporate strategies and performance. This suggests a number of hypotheses.
First, within industries, the firms most likely to engage in benchmarking are those which face the lowest costs in acquiring competitor information, for example, because they can spread the fixed costs of doing so over greater size; and/or because they are integrated into company groupings – such as multinational enterprises – that can secure comparative performance data from internal sources.
Second, there may also be an effect by which it is the ‘better’ managerial teams that make the greatest investment in securing comparative information, both because they stand to lose less from doing so and are better placed to act on the information they acquire.
Third, the incentives to engage in systematic comparisons may be greatest in larger firms, these being the firms for which agency costs are likely to be highest in the first place, and which, in the absence of international competition, are most likely to lack adequate domestic comparators.
In summary, there should be a relationship between firm and industry characteristics, the adoption of systematic processes of monitoring rivals, and corporate performance (for example, in terms of competitiveness on world markets). This relationship will be reinforced by the ‘sampling’ effects of greater product-market competition. In particular, entry by importers and the greater exposure of domestic firms to export markets will bring a larger range of alternative approaches and strategies into play. So too should contact with a more extensive set of customers and suppliers, who can act as valuable sources of market information and of technical support. All of this should result in accelerated learning, most notably by the firms directly involved in international trade but also, through spillover effects, by other firms in the industry.
4.2.2 Corporate practices, selection and efficiency
By tightening the product-market constraints bearing on managers, integration will also alter managers' abilities and incentives to perpetuate inefficient ways of doing things. Given the historical development of Australian manufacturing, four areas are likely to be especially important.
First, inefficient work practices are likely to come under pressure, as are the other mechanisms by which rents are shared between managers and other employees. One would therefore expect to see two effects jointly: managerial slack being reduced as agency costs are reduced; and equally, employee slack decreasing as a result of reductions in agency costs within firms. Tighter product-market constraints – a dwindling of the rents available for sharing – should make this process all the sharper.
Second, improved information and more intense selection may induce efforts to upgrade product quality.
Third, excess product variety, with its corollary of sub-scale production, could be perceived as a greater handicap. In effect, though product differentiation can dissuade new entrants, it is unlikely to be a successful strategy when it imposes a substantial cost disadvantage on domestic producers. The very broad product ranges typical of Australian industries could be expected to prove unsustainable in a more competitive environment.
Fourth, and interacting with the third point above, greater access to export opportunities, which effectively expands the market available to producers, should strengthen the incentives to exploit economies of scale. A larger market creates greater room for efficiently-scaled plants. The trade-off between carrying excess capacity at the time new plants are first introduced, and achieving lower unit costs through economies of scale over time, will tend to favour larger plants when the absolute size of the market is larger, given an independently determined growth rate of demand and producers acting on a stable pattern of oligopolistic interaction (Scherer et al. 1975). At the same time, access to export markets will tend to encourage more aggressive capacity expansion by low-cost producers. By allowing these producers a greater range of opportunities to displace less-efficient rivals, not only at home, but also abroad, it reduces the price fall necessary to accommodate the additional output their expansion entails.
Together, these factors should be reflected in a pattern in which the more efficient, export-oriented producers take the lead in seeking to implement new industrial relations arrangements, as well as in trying to secure the fullest benefit from economies of scale and scope.
4.2.3 Productivity and specialisation
The process within each industry which results from these forces should have four salient features.
First, as the most efficient producers self-select by leading in the adoption of more efficient ways of working, there might be, at least initially, a rising, possibly substantial, gap between firms within industries.
Second, the greater the barriers to the diffusion of new management practices, and the higher the costs of exit, the larger and more persistent this gap will be. We might, therefore, expect to find the convergence process within industries being slowest for industries or market segments where sunk costs are relatively high.
Third, given these disparities, the firms which perform best – in terms of productivity and competitiveness on world markets – should be those which have the greatest commitment and ability to learn. They would, in other words, bring together the factors set out above: orientation to benchmarking, and adoption of processes for systematically monitoring cost and quality relative to competitors; willingness to learn from foreign suppliers of technology and inputs; capacity to create an industrial relations climate sufficiently flexible to adapt to new ways of doing things; and access to the resources needed to implement change.
Finally, as this sorting process runs its course, Australian industries could become more specialised, reflecting not only the fuller exploitation of product-specific economies of scale, but also (and probably more importantly) managerial diseconomies of scope. Given a continuing (indeed, income-elastic) demand for diversity, rising intra-industry specialisation should result in greater intra-industry trade.
4.3 Testing
These hypotheses have been tested first by using the responses to the recent AMC survey and second, by analysing industry-level data on trade and output.
4.3.1 The AMC survey: background, overview and assessment of data quality
The survey was conducted over December/January 1993/94 and hence results may have been affected by either shutdowns over the Christmas period, or by seasonal work, for example, in the food industry. Aimed at firms with more than 20 employees, the survey was stratified across 12 ASIC/ANZSIC industry codes and three size categories (by employees: 20–49, 50–99 and over 100). Sampling frames were designed to ensure that all 36 cells had a minimum number of respondents. Overall, there were 962 respondents to the survey, equivalent to over 10 per cent of the population, sufficient to provide an adequate basis for analysis.
The survey contained over 100 questions, many of them involving scalar judgments (that is, the respondents were asked to rank themselves on a scale). It is consequently a very rich but complex database, with especially difficult problems being involved in disentangling the causal links between variables.
Given the number of questions, and the fact that some of the terms used in the survey may have been unfamiliar to the respondents, there is some concern that the quality of the results may have been affected by respondent fatigue. Two approaches were used to test for this:
- First, where similar questions have been asked in different parts of the questionnaire (in particular, where a question has been asked near the beginning of the questionnaire, when respondents are freshest, and a similar question is asked near the end), the correlation between responses has been examined.
- Second, where the tone of a question is different from that of the questions surrounding it (for example, because the surrounding questions involve replies where a higher value is ‘better’ than a lower value, while the reply structure for the question at issue goes in the other direction), the correlation between answers has been checked to see if the respondent was ‘awake’ to the change in scale.
The results of this analysis are reproduced in Table 4. As can be seen, for all the questions testing fatigue, except that on marketing costs (where the two questions asked are the least similar of those considered), there is a positive association in responses.[19] Equally, the questions involving a change in the direction of a scale exhibit a negative association. It therefore seems reasonable to conclude that the length and complexity of the survey did not seriously erode the quality of the replies.
Type of question | Survey references | Kendall's tau | Standard error |
---|---|---|---|
Tests of ‘fatigue’: | |||
Operations focused | PL6 and TE2 | 0.19 | (0.03) |
Just-in-time | FO1B and TE1P | 0.53 | (0.03) |
Production quality | MS3F and PO1F | 0.24 | (0.03) |
New products | MS3H and PO1G | 0.29 | (0.03) |
Materials | MS3D and PO1A | 0.13 | (0.03) |
Marketing | MS3K and PO1D | −0.03 | (0.03) |
Tests of ‘awareness’: | |||
Technology/HRM | MS4C and MS4D | −0.16 | (0.03) |
HRM/simultaneous | MS4D and MS4E | −0.11 | (0.03) |
The quality of the responses can also be tested by examining the concordance between firms' ranking of their performance on Likert-type scales with the rankings which emerge from comparisons of quantitative performance indicators. For example, firms were asked whether they considered themselves to be among the technological leaders in their industry. About 8 per cent of respondents rated themselves in this group. Analysis of these responses shows that the firms in this group do tend to score more highly on a range of performance indicators: they are more likely to export (about 46 per cent versus a 36 per cent average for all firms); and they do more R&D. Further, it is worth noting that these firms also rated themselves as having higher productivity growth rates and levels, were more likely to be foreign owned and were more likely to benchmark their performance against rivals (the association between a firm's rating of its ‘technological lead’ and these other variables was tested using Kendall's tau, all associations being significant at the one per cent level). This last point is especially significant because it suggests that the firms involved were relatively well-informed.
Potential response bias was investigated through a telephone survey of 108 firms that had not responded to the original postal survey. The results, which are reported in AMC (1994), found that non-respondents had higher self-assessed scores across a sub-sample of 8 questions drawn from the original postal survey. While this may be taken to imply that there is a non-response bias against the ‘better’ firms, it may also indicate a tendency to be overly optimistic in responses to telephone surveys. Nevertheless, the potential for some biases in this direction must be noted in interpreting the results presented below.
On balance, all of this gives some support to the view that the assessments reported in the survey are of reasonable quality, and these are consequently used below for statistical testing. For simplicity, in the presentation of the results below, the actual values of Kendall's tau, and its asymptotic standard error, are omitted. However, unless otherwise noted, the results reported are significant at the one per cent level.
4.3.2 The changing intensity of competition
An important element in the hypotheses set out above is the effect of greater integration on the intensity of product-market competition, which then alters firm conduct and performance.
However, the survey provides little indication of the competitive conditions in which firms operate. Firms were asked to report their market share – which even at the best of times is a poor indicator of market power – but there was a high non-response rate to this question, and those firms which responded appear to have done so using quite different conceptions of the relevant market. As a result, indicators of competitive conditions had to be derived from other sources. Estimates have been made of the trade-adjusted Herfindahl-Hirschman indices (HHIs) of concentration at the industry level using the methodology set out in Appendix C; but these will overstate market power in industries where entry barriers are low, and may understate it where markets are geographically fragmented.
These problems extend to assessing the degree to which firms are, or feel, constrained by international competition. Since the survey does not contain specific questions in this regard, appropriate indicators have had to be constructed. Two are especially important.
The first are time series on import penetration (see Figure 5, above). In particular, an effort has been made to develop a time series of import penetration at the industry level corrected for the consumption of own-industry intermediate inputs (methods and main results are described in Appendix B). Though these measures are an improvement on those normally used, they still have serious weaknesses.[20]
Second, the import-penetration measures have been supplemented by using measures of manufacturers' perceptions of the intensity of import competition. The primary source is the quarterly Survey of Australian Manufacturing carried out by the AMC since June 1989, the main results of which are summarised in Table 5.[21] The survey asks firms whether they believe import competition has increased in the last quarter, and hence responses are likely to be quite sensitive to exchange rate conditions. Three points can be drawn from the data set out in the table:
1989/90 | 1990/91 | 1991/92 | 1992/93 | 1993/94 | |
---|---|---|---|---|---|
Food, beverages and tobacco | 11.7 | 9.3 | 13.3 | 5.3 | 4.0 |
Textiles | 12.5 | 15.8 | 17.7 | 27.3 | 31.3 |
Clothing and footwear | 32.0 | 35.8 | 40.3 | 49.5 | 27.7 |
Wood products | 2.8 | 16.5 | 14.5 | 11.8 | 9.0 |
Paper products | 4.3 | 9.3 | 8.3 | 9.3 | 3.7 |
Chemical and petroleum products | 15.9 | 20.3 | 29.6 | 21.8 | 16.3 |
Non-metallic mineral products | 10.2 | 2.8 | 15.2 | 12.8 | 15.7 |
Basic metal products | 1.2 | 18.5 | 22.4 | 19.5 | 10.7 |
Fabricated metal products | 15.0 | 12.4 | 11.2 | 13.5 | 7.7 |
Transport equipment | 21.9 | 11.8 | 12.3 | 8.3 | 5.3 |
Other machinery and equipment | 20.8 | 23.7 | 19.8 | 22.8 | 19.0 |
Miscellaneous manufacturing | 18.4 | 24.2 | 20.6 | 12.5 | 9.7 |
Total manufacturing | 12.9 | 15.3 | 17.7 | 15.8 | 11.7 |
Note: 1993/94 data are estimates based on three-quarters to March. Source: Australian Manufacturing Council, Survey of Australian Manufacturing. |
- The consistently positive numbers indicate that competition from imports has been continuously increasing since 1989, despite the fact that this post-dates the largest declines in protection.
- The greatest increases appear to have occurred in Clothing, Chemical and Petroleum Products, and Basic Metals. Transport Equipment, in contrast, has relatively low figures, which may reflect both continued protection and the fact that many of its imports are controlled by the domestic producers.
- The fall in some of the measures in 1993 may be due to the weaker exchange rate.
Interestingly, there is little correlation between the series on import penetration and that on perceptions of the intensity of import competition. This suggests that the distinction between arms-length imports on the one hand, and related-party imports on the other, may be significant in explaining differing degrees of product-market contestability.
For example, as shown in Figure 9, in the Paper Products, Transport Equipment, and Basic Metal Product industries, the proportions of firms responding that import competition has increased are lower than one might expect given the observed change in import penetration. This may indicate the relatively small proportion of competing imports in these industries. In contrast, perceptions of increased import competition appear greater than actual increases in penetration in the Chemical and Petroleum Products and Non-Metallic Mineral Products industries. This may reflect greater degrees of contestability in these markets.[22]
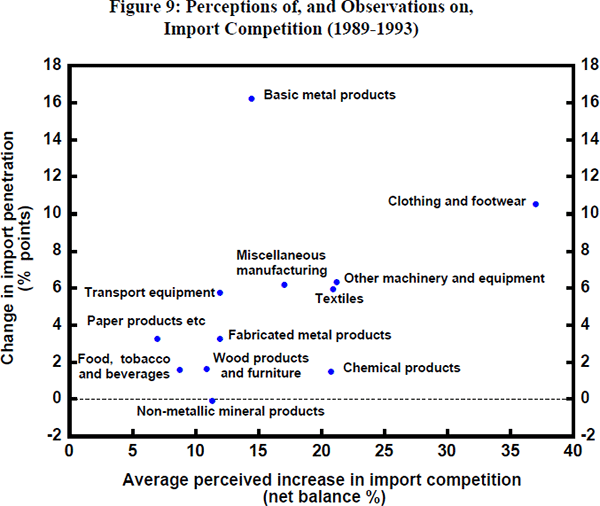
4.3.3 Integration, learning and performance
Given this background, four results associating internationalisation, learning and corporate performance emerge with some strength from the work carried out to date.
First, the firms most likely to systematically monitor the performance of their rivals are those most engaged in the international economy.
This is suggested by examining the responses to questions about whether the firm has mechanisms in place to benchmark its performance relative to competitors and, if so, how much time senior management devotes to this task. Replies to these questions show that export-focussed firms (that is, firms listing a foreign market as among their top two priorities) are more likely to benchmark (58 per cent having policies to this effect as against 40 per cent of the remaining group). In contrast, regionally-focussed firms (that is, firms selling largely within their own State), are less likely to benchmark. In addition, US and Japanese-owned firms, which presumably can secure high quality comparative information from internal sources, are far more likely to benchmark than any other category of firm, including those which are Australian-owned.
The results also show that larger firms make greater use of benchmarking than their smaller counterparts, possibly reflecting a higher incentive to benchmark (given higher agency costs in the absence of systematic performance comparisons) and the fixed costs involved in securing competitive information. Other than through international involvement, we find little relation between the frequency of benchmarking and the competitive conditions in which firms operate.
Second, firms engaged in the international economy are also most likely to focus on customer satisfaction and on product quality.
Exporters gave a higher score to the five questions measuring the effort devoted to monitoring customer satisfaction than did other firms. This is also true of foreign-owned firms. Exporters were also more likely to focus on controlling product quality, with significant positive relationships on all but one of the four variables in the survey aimed at capturing the investment firms make in this respect. Here too, the links primarily work through exporting, with the intensity of competition having little effect on performance.
Third, being engaged in international markets is also the primary factor which allows firms to extend their sources of information and learning.
Regardless of competitive conditions in the industry, exporters are more likely than domestically-oriented firms to find their customers to be of at least some assistance in achieving world-best practice (64 per cent versus 56 per cent for non-exporters). Exporters are also far more likely than other firms to respond that overseas firms have been an important source of assistance. The relationship persists even after accounting for the role of customers and suppliers, probably reflecting the impact of exposure to a broader range of competitors.
Foreign-owned firms are more likely to regard their parents as a source of technical assistance than are Australian firms owned by multi-unit parents. However, even removing the impact of assistance from foreign parents, there remains a strong association between foreign ownership and assistance from foreign firms. This may reflect the impact of management structures in foreign subsidiaries, which perhaps provide for more effective learning. Also important may be the higher R&D intensity of foreign firms, which is likely to increase their information about best practice and reduce the costs involved in identifying overseas sources of technical help.
It is, however, worth noting that subsidiaries of foreign firms, though they regard their parent as a valuable source of advice, also frequently regard it as a barrier to achieving improved performance (37 per cent of foreign firms regard their parent as a barrier – compared with 23 per cent of the domestic firms owned by multi-firm entities). Importantly, the two views are often held jointly – 38 per cent of the foreign firms that found their parents of assistance also regarded them as a barrier. This suggests that the barriers in question may involve restrictions on the use in export markets, of the skills and capabilities obtained from the parent. We return to this point below.
Fourth, learning and the international diffusion of technological progress are also likely to have been assisted by the declines in protection of imported capital goods.
The Industries Commission estimates that the effective rate of assistance (ERA) on imports of industrial machinery and equipment (taking account of concessions for imported capital) fell from over 40 per cent at the start of the 1970s, to around 13 per cent by 1992/93. This process is especially important because it directly benefits some parts of the non-traded sector which are large importers of such equipment – the ABS estimates that more than half of the gross fixed capital expenditure of firms in the finance, property and business services and wholesale trade sectors is imported. Arguably, the diffusion of technological progress through its embodiment in capital goods is likely to be more important in imports of advanced technology. Table 6 shows the importance of imports to 22 categories of advanced manufacturing technologies. Imports were the source of over half of such items in all but one of the technology classes. Furthermore, the importance of imports as a source of such technology seems to be increasing.
1988 | 1991 | |
---|---|---|
Design and engineering: | ||
Computer-aided design (CAD) and/or engineering (CAE) | 54 | 76 |
CAD output used in control manufacturing machines | 63 | 75 |
Digital representation of CAD output used in procurement activities | 46 | 66 |
Fabrication, machining and assembly: | ||
Stand-alone NC/CNC machines | 84 | 88 |
Flexible manufacturing cells or systems | 66 | 72 |
Materials working lasers | 62 | 79 |
Advanced cutting technologies apart from lasers | 51 | 64 |
Advanced joining and coating technologies apart from lasers | n.a. | 81 |
Advanced treatment apart from lasers | n.a. | 59 |
Filament winding, reaction injection moulding, pultrusion, and/or casting | n.a. | 46 |
Simple pick and place robots | 65 | 64 |
Other more complex robots (those used for spot or arc welding) | 65 | 86 |
Other more complex robots (those used for assembly, finishing or other applications) | 84 | 82 |
Automated material handling: | ||
Automatic storage and retrieval systems | 58 | 57 |
Automated guided vehicle systems | 70 | 66 |
Automated sensor-based inspection and/or testing equipment: | ||
Performed on incoming materials or in process | 63 | 78 |
Performed on final product | 64 | 66 |
Communications and control: | ||
Local area computer network for technical data | 60 | 72 |
Local area computer network for factory use | 52 | 68 |
Programmable logic controllers | 63 | 77 |
Intercompany computer network linking plant to subcontractors, suppliers and/or customers | 53 | 56 |
Computers used for control on the factory floor | 59 | 75 |
Source: ABS Cat. No. 8123.0. |
In short, involvement with international markets does appear to be associated with greater and more systematic learning. It is highly likely that in practice, the causality runs both ways, creating positive feedback loops to the benefit of outward-oriented firms.
4.3.4 Corporate practices, selection and efficiency
Improvements in management incentives and information, combined with the rigours of a more demanding selection environment, should put intensified pressure on inherited inefficiencies. Out of the broad range of results derived from analysing the survey, three can be used to examine these impacts.
First, firms' efforts to upgrade their product quality appear to be related to their involvement in the international economy.
The survey asked firms to rate their product defect rate relative to competitors, and to report the share of defective products in their product volume. Using the responses, we classified firms into two groups: those with low product quality and those with high product quality. We then estimated a probit model using variables from the survey as explanatory variables. The results are reported in Table 7. A positive coefficient indicates that the relevant variable makes it more likely that the firm is a high-product-quality firm.
Variable | Relative defect rate | Defects/volume | ||
---|---|---|---|---|
Constant | 0.11 | (0.29) | 0.42 | (1.13) |
Industry dummies: | ||||
Food, beverages and tobacco | 0.30 | (1.40) | 0.44 | (2.15) |
Textiles | −0.22 | (−0.71) | −0.37 | (−1.16) |
Clothing and footwear | 0.32 | (1.31) | 0.23 | (1.00) |
Wood products | 0.67 | (2.84) | 0.18 | (0.80) |
Paper products | 0.02 | (0.11) | −0.09 | (−0.42) |
Chemical and petroleum products | −0.41 | (−1.54) | 0.34 | (1.32) |
Non-metallic mineral products | −0.31 | (−1.02) | −0.56 | (−1.69) |
Basic metal products | −0.49 | (−1.46) | −0.09 | (−0.32) |
Fabricated metal products | −0.18 | (−0.91) | 0.47 | (2.38) |
Transport equipment | 0.14 | (0.52) | 0.52 | (1.92) |
Other machinery and equipment | −0.17 | (−0.76) | 0.57 | (2.67) |
Foreign ownership | 0.42 | (2.81) | 0.27 | (1.85) |
Parent restrictions | −0.19 | (−1.26) | −0.98 | (−6.50) |
R&D/sales | −0.002 | (−0.07) | −0.14 | (−3.97) |
Size | −0.27 | (−3.67) | −0.26 | (−3.78) |
Export | 0.06 | (0.49) | 0.12 | (1.04) |
Adopted any advanced technology | — | — | −0.23 | (−1.79) |
Customer focus in design | −0.22 | (−1.35) | −0.52 | (−3.31) |
Measure quality | 0.20 | (2.18) | 0.09 | (1.04) |
Standardised procedures | 0.15 | (2.55) | 0.09 | (1.58) |
Pay-for-performance scheme | 0.002 | (1.36) | −0.0008 | (−0.68) |
Number of trade unions | −0.07 | (−1.56) | −0.03 | (−0.80) |
Number of quality inspectors | −1.70 | (−1.86) | 0.73 | (0.85) |
Frequent review of cost of quality | −0.08 | (−1.70) | −0.07 | (−1.47) |
Frequent review of customer satisfaction | 0.05 | (1.00) | 0.13 | (3.06) |
Likelihood ratio | 76.64 | 167.72 | ||
Per cent correctly predicted | 64.86 | 69.91 | ||
Note: t-statistics are in parentheses. |
The results suggest that firms in industries with higher levels of protection tend to have lower product quality, as do those in industries which have recently experienced large reductions in protection. Size also tends to be associated with lower relative product quality, as is industrial concentration measured by the estimated HHI.
Foreign ownership is the single variable most strongly associated with higher product quality. However, those subsidiaries which report that they are subject to parent-company restrictions limiting their competitiveness (the ‘parent restrictions’ variable in the model) tend to have significantly higher product defect rates, possibly as a result of foregone learning economies. Some management practices are also associated with higher product quality, notably the efforts the firm makes to measure product quality, the extent to which it has standardised procedures for controlling quality, and the frequency with which it reviews customer satisfaction.
The negative and significant coefficients on the number of quality inspectors and on frequency of review of the cost of product quality, and equally negative but not significant coefficients for R&D intensity and customer focus in design, suggest that these measures may have been introduced in response to problems with quality in the first place. The coefficient on exporting is also positive but not significant.
Second, the firms most oriented to international markets seem to be among the leaders in industrial relations reform.
In a probit model explaining exports (discussed in greater detail below), there is a positive association between export involvement and having an enterprise agreement. Moreover, exporters are much more likely to rate their enterprise agreement as effective, as well as to respond that unions have a positive role in their plants – possibly reflecting greater willingness by unions to cooperate in the face of tighter product market constraints. Nonetheless, exporters are more likely to regard the current industrial relations system as a constraint on their performance.
A similar pattern holds for foreign-owned firms, which, like exporters, are more likely to have an enterprise agreement, more likely to regard it as effective, and more likely to view unions as having a positive role in their plants. Foreign-owned firms appear slightly more likely to introduce gain-sharing, productivity-related pay and piece rates. This may be related to the fact that these firms use different technologies from their Australian-owned counterparts, and notably seem to make greater use of advanced manufacturing techniques.
Third, there is some, albeit mixed, evidence linking protection to excess product variety, though less so to foregone economies of scale.
Firms were asked whether they thought they produced too many product varieties or perceived their size to be a barrier in competition. As far as product variety is concerned, the sectoral pattern is complex but suggestive. Transport Equipment, despite its high levels of protection, has the lowest rate of respondents considering excess product variety to be a problem. This may well reflect the incentives which have been provided under the Passenger Motor Vehicle Plan to reduce the number of models each firm produces in Australia. Partly as a result of these incentives, the number of Australian-made models has fallen from 13 in 1985 to 6 today. Once the Transport Equipment industry is removed, the relationship between the level of the effective rate of assistance and the frequency with which firms in an industry report excess variety as a problem, becomes significantly positive.
An equally complex pattern emerges in respect of economies of scale. Fewer than 30 per cent of firms regard themselves as handicapped by the scale of their operations. Interestingly, the highest proportion of these is in chemicals, which has relatively low ERAs now but was highly protected until the late 1970s. Since that time, the industry has experienced relatively slow rates of domestic demand growth and sharp increases in import penetration, which may have limited the ability to exploit scale economies. There is also some clustering of positive responses in the highly protected clothing and footwear industries, possibly capturing firms' perception that long-run survival will depend on their ability to offset a labour-cost disadvantage through greater scale economies. However, firms producing transport equipment and textiles do not consider themselves to be sub-scale.
Overall, in a probit model including size, foreign ownership, whether the parent company imposed barriers on the affiliate, an estimate of the Minimum Efficient Scale (MES) and whether firms are automated, an increase in the ERA increases the likelihood of scale being viewed as a barrier but the coefficient is not significant.[23]
In considering these results, it is worth noting the uncertainties which surround the extent and significance of scale economies.
Recent studies find, for example, that even in industries in which scale economies seem substantial, there is considerable entry by firms operating far below MES (Acs and Audretsch 1988, 1989). Though Schumpeterian selection may ensure that some of these firms disappear while others eventually expand to MES, it also seems to be the case that a not insignificant proportion survive while remaining below the MES threshold. This suggests that scale penalties are either smaller than the conventional MES estimates suggest and/or can be offset by other factors such as superior product quality, higher market flexibility and better customer service.
Moreover, technical change may be reducing MES in many industries. Though the evidence is largely anecdotal, the hypothesis gets some support from overseas trends in the size distribution of firms. A similar pattern emerges for Australia, as can be seen from the evidence on the changing size distribution of Australian plants presented in Figure 10. In every industry, the average number of employees per firm has fallen over the past 15 years, in many cases substantially. Furthermore, the distribution of employment per firm has become more positively skewed as the number of small firms has increased. This may reflect rapidly rising labour productivity in the larger firms (which could imply an increase in the MES); but it seems difficult to believe that there would be so uniform a trend away from employment in larger plants if substantial parts of Australian manufacturing were seriously sub-scale. The ‘conventional wisdom’ that Australian manufacturing plants are too small may consequently need to be re-examined.
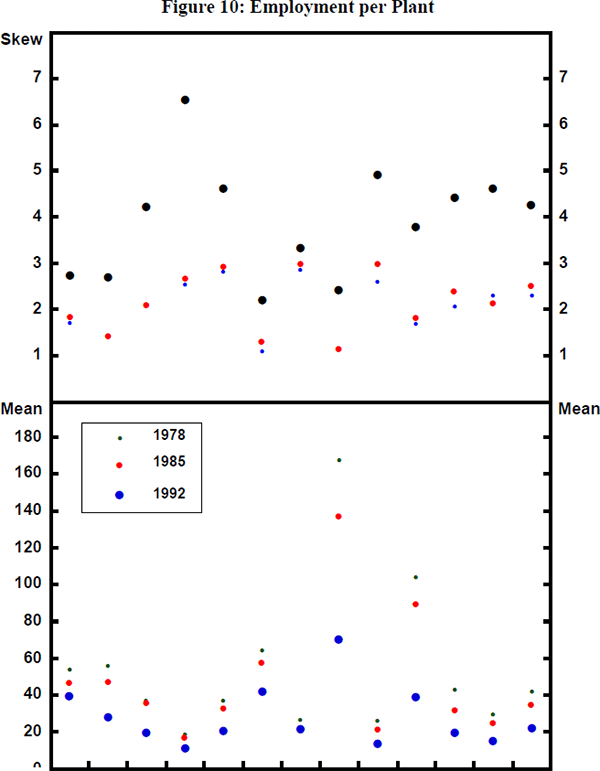
4.3.5 Competition, productivity, export performance and specialisation
All of this highlights the many and diverse respects through which international involvement alters corporate conduct; the key issue then is how this translates into differences in performance. Six results of the analysis are worth emphasising here.
First, there appears to be a rising dispersion in performance within industries.
This rising dispersion is most evident in the information available on labour productivity (data on capital stocks are not available for individual firms). In particular, we have used data on employment and output to compute average productivity levels for each size-class of firms, as a basis for calculating the coefficient of variation of within-industry productivity.[24] The results show that for almost all of the 12 2-digit industries the coefficient of variation increased over the period 1978–1992. This result also emerges from a regression of the survey data on productivity levels (together with other variables) against the survey responses on productivity growth rates, yielding a significant positive coefficient. It can be supposed that this reflects the differing capacity of firms to make the transition to a more open environment; but as the disparities open up, they may well be accentuated by the more frequent shocks, notably resulting from supply-side innovations,[25] which can be expected to characterise a competitive, internationally exposed economy.
Second, dispersion appears to be greatest in industries which are highly concentrated and which are either now highly protected, or were so until recently.
It is reasonable to expect dispersion to be greatest in industries which are sheltered from domestic and international competition – that is, industries where high entry barriers ensure that the inefficiencies encouraged by trade protection are not rapidly undermined by competing domestic entry. This presumption is strengthened by the likelihood that adjustment to reductions in assistance will be a long and drawn-out process in industries in which sunk costs are high (since these make exit costly). The analysis bears this presumption out, since the intra-industry dispersion in relative unit costs is strongly positively related to the product of the HHI and the ERA (the correlation coefficient between these being 0.34).[26]
Third, the factors which most sharply differentiate firms within industries in terms of their relative unit costs are intangible investment, specialisation and industrial relations.
This is suggested by the probit regression model for relative unit costs presented in Table 8. Since a higher number implies lower costs than those of rivals, positive (negative) coefficients refer to variables which increase (reduce) competitiveness. Investment in knowledge (as measured by the ratio of R&D to sales) and in people (as measured by training expense relative to payroll) are more significant determinants of competitiveness than are investments in automation, or the use of advanced technologies (which has a negative, albeit insignificant, coefficient). While the evidence is relatively weak, it is consistent with the argument that intangible assets – such as skills and know-how – are idiosyncratic and difficult to imitate, and hence provide a greater differentiating factor than do other forms of investment.
Variable | Industry dummies | Industry averages | ||
---|---|---|---|---|
Constant | −1.91 | (−3.70) | −2.64 | (−3.02) |
Industry dummies: | ||||
Food, beverages and tobacco | 0.29 | (0.99) | — | — |
Textiles | 0.80 | (2.32) | — | — |
Clothing and footwear | 0.42 | (1.34) | — | — |
Wood products | 0.85 | (3.11) | — | — |
Paper products | 0.68 | (2.23) | — | — |
Chemical and petroleum products | 0.43 | (1.33) | — | — |
Non-metallic mineral products | 0.56 | (1.55) | — | — |
Basic metal products | 0.16 | (0.42) | — | — |
Fabricated metal products | 0.47 | (1.88) | — | — |
Transport equipment | 0.50 | (1.51) | — | — |
Other machinery and equipment | 0.32 | (1.17) | — | — |
Good enterprise agreement | 0.18 | (1.07) | 0.18 | (1.14) |
Pay-for-performance | −0.003 | (−1.92) | −0.003 | (−2.09) |
Advanced technology | −0.07 | (−0.37) | −0.03 | (−0.16) |
R&D/sales | 0.08 | (1.75) | 0.06 | (1.55) |
Size | 0.02 | (0.20) | −0.005 | (−0.06) |
Constraints on finance for capital | −0.48 | (−3.52) | −0.50 | (−3.73) |
Too diversified | −0.23 | (−1.75) | −0.25 | (−1.93) |
Too small | −0.37 | (−2.46) | −0.43 | (−2.99) |
Utilise capital effectively | 0.41 | (2.94) | 0.43 | (3.24) |
Training expense | 0.05 | (1.34) | 0.05 | (1.28) |
Automation | 0.07 | (0.96) | 0.07 | (1.03) |
Work team | 0.15 | (2.31) | 0.16 | (2.51) |
Does not benchmark | −0.03 | (−0.24) | −0.05 | (−0.38) |
Government as customer | −0.19 | (−1.34) | −0.15 | (−1.11) |
No trade union | 0.62 | (3.83) | 0.57 | (3.75) |
Industry average relative unit cost | — | — | 0.46 | (1.60) |
Likelihood ratio | 92.64 | 79.41 | ||
Per cent correctly predicted | 73.63 | 73.15 | ||
Note: t-statistics are in parentheses. |
The worst performers seem to be firms which feel they are too small, produce too many products, and do not have the capital to expand. An inability to use capital effectively, which is likely to be related to inadequate specialisation and/or industrial relations constraints, is also a highly significant drag on cost competitiveness. The results also suggest that firms without unions tend to have significantly and substantially lower costs. For firms which do have unions, having a ‘good’ enterprise agreement partly offsets the cost penalty. Using work teams tends to reduce costs while pay-for-performance tends to increase them (though the causality here may well run from having higher costs to adopting pay-for-performance).
There is some evidence of intra-industry spillover, perhaps through demonstration effects. This can be seen by replacing the industry dummies by the industry average response to the question on relative unit costs, as is done in the second column of the table. The other coefficients remain stable while the industry average term is positive and significant at just over the 10 per cent level on a 2-sided test.
Fourth, one aspect of the disparities in the firm performance is the presence of a large tail of firms – accounting for just under 30 per cent of firms and 20 per cent of employment – which carries out little or no R&D, undertakes no benchmarking and does not export.
These firms are most likely to be selling intermediate inputs, generally in regional markets. Typically they also have poorer cash flow than other firms and lower (self-assessed) rates of growth of productivity.
Fifth, export competitiveness at the level of the firm appears to be strongly influenced by relative unit costs, but is also affected by size, ownership, benchmarking, technological capability and emphasis on quality. As has been argued above, many of these variables ultimately seem to hinge on the firm's exposure to, and willingness and ability to learn from, world-best practice.
Table 9 reports a probit model on export orientation, defined as whether a firm lists a foreign market as among its top two priorities. All the variables have the expected sign, and the model correctly predicts, within sample, over 72 per cent of the observations.
Variable | Probit estimate | |
---|---|---|
Constant | −3.34 | (−5.39) |
Industry dummies: | ||
Food, beverages and tobacco | 0.30 | (1.33) |
Textiles | 0.69 | (2.26) |
Clothing and footwear | 0.44 | (1.67) |
Wood products | 0.17 | (0.69) |
Paper products | −0.59 | (−2.24) |
Chemical and petroleum products | 0.27 | (0.99) |
Non-metallic mineral products | −0.64 | (−1.86) |
Basic metal products | 0.07 | (0.23) |
Fabricated metal products | 0.35 | (1.63) |
Transport equipment | 0.27 | (0.92) |
Other machinery and equipment | 0.17 | (0.75) |
Foreign ownership | 0.44 | (2.90) |
Parent restrictions | −0.28 | (−1.85) |
R&D/sales | 0.17 | (4.89) |
Size | 0.15 | (2.15) |
Training expenditures/payroll | 0.12 | (0.90) |
Customer relation is top priority | 0.05 | (1.16) |
Customer complaint resolving process | 0.02 | (0.32) |
Quality is top priority | 0.07 | (1.15) |
Suppliers located overseas | 0.30 | (1.94) |
Measures quality of output | 0.26 | (3.24) |
Far away from quality certification | −0.02 | (−0.39) |
Possesses an advanced technology | 0.47 | (3.04) |
Does not benchmark | −0.27 | (−2.40) |
Has an enterprise agreement | 0.19 | (1.55) |
Defect/volume rate | −0.10 | (−1.13) |
Relative unit costs | 0.21 | (3.46) |
Likelihood ratio | 193.23 | |
Per cent correctly predicted | 72.46 | |
Note: t-statistics are in parentheses. |
Even correcting for other factors, large firms are more likely to be exporters than are small firms. This confirms the results of the cross-tabulation analysis, which showed that 46 per cent of the firms with more than 100 employees were export oriented, as compared to under 25 per cent of those in the smallest size class (50 employees or less). Foreign ownership also remains a significant factor increasing export orientation. However, the effect can be offset, at least partly, by parent company restrictions; respondents stating that they were subject to such restrictions having significantly lower export propensities. As noted above, 37 per cent of the foreign firms reported being subject to parent company restrictions – those doing so comprising 47 per cent of the US-owned firms, 33 per cent of the UK-owned firms but only 18 per cent of the much smaller number of Japanese-owned firms. These differences may be related to differences in access to parent-company technology, but it has not yet been possible to test this hypothesis.
Technological capability, as measured by the ratio of R&D to sales and by possession of an advanced technology, has an effect on the propensity to export, above and beyond its effect on relative unit costs. In addition to product differentiation this may also be because firms which invest heavily in technical know-how are more likely to be aware of broader market trends.
Quality also appears to play a significant role in export orientation. Here too the commitment to monitoring performance – proxied in this context by whether the firm systematically measures the quality of its products – seems particularly important. Firms which benchmark are also more likely to be export oriented, as are firms which are heavily involved with, and rely on, foreign suppliers.
Finally, it is worth noting that when the other factors affecting export orientation are taken into account, the Transport Equipment industry does not appear to be especially export oriented – despite the large-scale export assistance which this industry receives.[27] The dummy on Transport Equipment, though positive, is not higher than those for a range of industries which are much less heavily assisted.
Sixth and last, the processes discussed above appear to have been paralleled by a move to greater specialisation within industries, presumably reflecting the sorting out of ‘good’ from ‘bad’ firms, and the elimination of excess product variety.
The AMC survey itself does not provide information on changing patterns of intra-industry specialisation. Nonetheless, an indicator of the trends in this respect can be obtained by examining trends in intra-industry trade, since they can be expected to capture the survival, and perhaps expansion, of those products within each industry in which Australian firms are competitive, and the contraction, and perhaps disappearance, of those in which they are not.
Two approaches have been used to examine trends in intra-industry trade. The first relies on the separation of imports into ‘competing’ and ‘non-competing’ classes (the former referring to imports which are similar to goods produced domestically, and the latter, to those which are not).[28] Madge, Bennett and Robertson (1989) present data on the ratio of ‘competitive’ to total imports from 1973 to 1987. These results confirm the intra-industry specialisation hypothesis – the ratio fell in 28 out of 41 3-digit industries examined. However, in a small number of cases, the largest falls in the ratio were experienced in the late 1970s with some beginning to rise towards 1987. The absence of more recent data inhibits identification of whether this is a change in the trend of the series.
The second approach relies on trade data reclassified into industry categories to calculate Grubel-Lloyd indices of intra-industry trade.[29] The results are set out in Figure 11, first calculated on the basis of volume data at the 2-digit level beginning in 1978, and then using data expressed in current values at the 4-digit level for the period from 1981/82 (highly disaggregated data not being available prior to that date on an industry basis). While it is clearly preferable to work with volumes, the value data are subject to less aggregation bias. Indeed, aggregation can produce very large differences in the level of the series, in particular for textiles and wood products. However, aggregation has less of an effect on changes in the indices. Both series provide strong support for the hypothesis of increased intra-industry specialisation, with the Grubel-Lloyd indices rising for almost all industry groups.
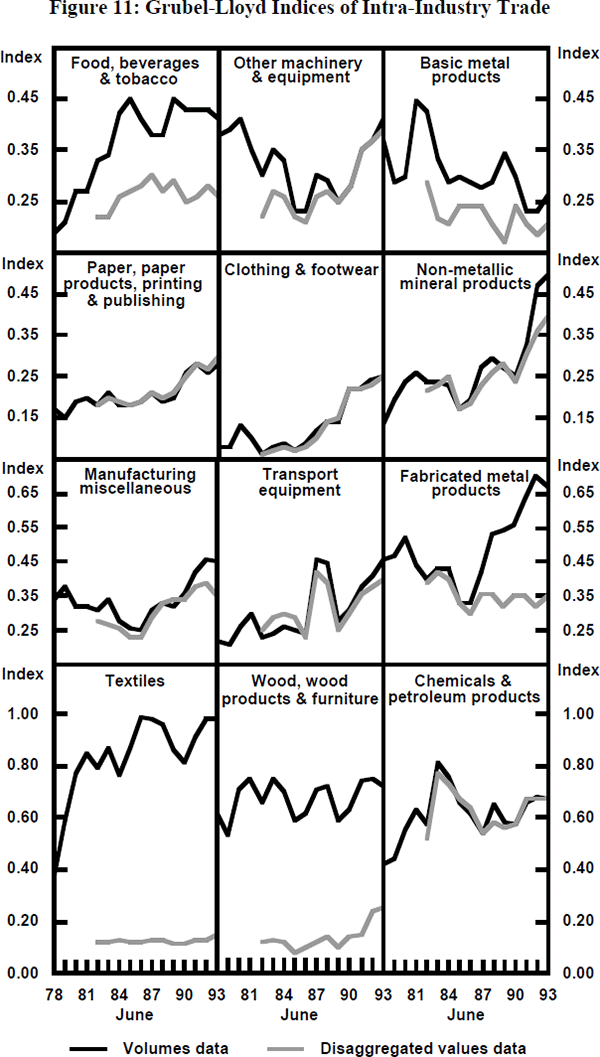
4.3.6 Concluding remarks
Taken as a whole, these results point to far-reaching change. Change, however, is not an objective in its own right; rather, it is valued because it contributes to improved productivity, and thereby creates scope for sustainable increases in living standards. It is, after all, an essential part of the case for trade liberalisation that, in the words of the seminal paper by Samuelson, ‘although it cannot be shown that every individual is made better off by the introduction of trade, it can be shown that through trade every individual could be better off, or in the limiting case, no worse off’ (Samuelson 1939, pp. 204).[30]
The evidence reviewed above cannot prove that the changes which have occurred pass the compensation test of welfare economics. Considerable adjustment is indeed underway, and its main features seem consistent with the broad goals of reform, but at least three observations need to be made.
First, there are obvious methodological limits to the analysis. As has already been noted, the cross-sectional relationships examined through the AMC survey are inherently complex, and further exploration of their causal structure is needed before it can safely be concluded that altering the trade exposure variables would produce the desired changes in performance.
Second, even with the rather large datasets available, there are many things which remain unexplained. It is a familiar finding of empirical research at a micro level that the factors which distinguish more from less successful organisations cannot be pinned down completely, regardless of how many control variables are factored into the analysis.[31] For example, 30 years of research on the factors determining school performance has tended to converge on the conclusion that the key element is leadership – a conclusion which, though it would hardly have been unpalatable to economists as diverse as Marshall, Pareto and Schumpeter, provides little comfort to would-be social engineers.
Third, the findings provide only limited support for those versions of the analytical arguments, summarised at the start of this section, which emphasise the role of intensified competition in generating increases in productive efficiency.[32] Competitive conditions, though, do play a significant role in determining product quality and in reducing intra-industry dispersion in performance. However, by far the strongest relationships found in this paper link superior performance to export orientation – not to competition per se. Several factors may be at work.
- This relationship may partly reflect the lack of an accurate indicator of the market conditions facing individual firms and, in particular, of the intensity of competition. Though this explanation is attractive, the range of indicators tried suggests that it is not very powerful.[33]
- To the extent that competition affects all firms in an industry, but exporting only affects those which have superior features and are best placed to adjust, we would expect the link to other dimensions of performance to be stronger for the latter, than for the former. However, this explanation, though attractive, may have less power than it seems. After all, especially when set against such a large sample, it would merely point to a weaker relationship between competition and performance than that found between export orientation and performance – not to an absence of a relationship altogether.[34]
- More plausibly, export orientation involves a substantial amount of self-selection: it is presumably the ‘better’ firms which accept the challenge of entering markets overseas. The fact that the links to performance seem to depend on whether or not the firm is export oriented, rather than on the amount of its exports, supports this view of export orientation as a shift variable signalling better managerial quality.[35] At the same time, of course, exporting very probably exposes the firm to new learning opportunities, which then serve to make the better firms even stronger.
- Finally, it may well be that export orientation pays particularly large dividends in terms of performance and notably in terms of learning.[36] This has often been suggested in the context of the dynamic Asian economies, and may plausibly also have been at work in the productivity surge in post-war Europe.[37] Much as it is sometimes claimed that successful industrialisation in a number of East Asian countries combined protection of the domestic market, with strong inducements to export, this effect may be quite independent of competition in the domestic market. Rather, the argument runs that the (at least partly) sheltered conditions in the domestic market provided firms with the resources required to compete vigorously overseas. The productivity benefits of the latter, outweighing the costs of the former, the outcomes were supportive of rapid economic expansion.[38]
5. Policy Implications
In market economies, firms are the primary focus of activity. Yet firms differ greatly, and in ways which are often difficult to explain. A great deal of recent work in economics emphasises this heterogeneity within industries, and tries to analyse its causes and consequences.
The work reported on here also emphasises these differences, which then play a major role in understanding the response to the increasing international integration of the Australian economy.
Seen from a societal point of view, many of these differences in firm behaviour are inevitable and some are positively desirable – since it is impossible to know in advance which response to change will ultimately prove most successful. Nonetheless, the persistence of a large tail of firms which seems to operate far from best practice, makes little effort to monitor efficiency and has little involvement in the international economy, could be a cause for concern.
It is interesting in this respect to compare the replies to the AMC survey with those of a recent, and as yet unpublished, survey of manufacturing firms carried out by the World Bank. In particular, in the World Bank replies for Japan, Korea and Taiwan, the gap in performance between the firms which considered themselves as technology leaders and others is considerably smaller than it appears to be in Australia.
In part, this may simply reflect different points on the adjustment path – and so be viewed as a problem which will prove largely self-correcting. But it may also be amenable to policy action aimed at accelerating the rate at which large gaps between best and average practice are narrowed.[39] Three options, which might be seen as mutually reinforcing, may be identified in this respect.[40]
A first is to ‘toughen’ the selection environment in which firms work. The evidence reviewed above does provide some support for this option, since there is a relationship between the intensity of competition and the extent of inter-industry dispersion in firm performance (although not the level of that performance). Going by the AMC survey, many of the ‘lagging’ Australian firms survive in regional markets, where competitive disciplines are most likely to be weak. While competition cannot be said to be a panacea, further progress in removing the impediments to trade between the States should induce greater and more rapid change among this part of the corporate population – including exit by those firms whose long-run prospects are poorest.[41]
A second option is to seek to strengthen the capabilities of lagging firms to catch-up. Access to technical competence is a case in point. A very high fraction of Japanese, Korean and Taiwanese firms surveyed by the World Bank make significant use of industrial extension services and of practically-oriented technical institutions (such as the Prefectural Laboratories in Japan or ITRI and CPC in Taiwan). These too are surely no panacea, but there may well be lessons here for making more effective use of the resources currently devoted to National Industry Extension Service and to the CSIRO.
Finally, a third option involves better identifying and easing the obstacles firms face to greater involvement with international markets. A specific question in this respect is asked in the AMC survey: and a major obstacle identified related to exchange rate uncertainty – with export-oriented firms seeing this as a greater problem than did their domestically-oriented counterparts. It is perhaps too easy to dismiss these views as reflecting a lack of understanding of the relevant options – after all, there is no reason to view firms as more ignorant in this respect than they are in others. The challenge then is to take these perceptions seriously, while recognising that for this problem, as for the others dealt with in this paper, there are simply no magic answers.
Appendix A: Trade Equation: Concepts, Sources and Methods
The equation was estimated using data for 1975, 1980, 1985 and 1990 by SUR. Inspection of the data suggested that different country groups had different intercepts, and that the relation between protection and trade intensity also differed across country groups. As a result, shift and slope dummies were included to allow for these different relationships. The differing relationship between protection and trade intensity may reflect the inadequacy of our measure of the former (based on tariff-receipts data) and regional differences in non-tariff barriers.
Across and within equation restrictions were tested. The restrictions that the coefficients on real GDP and real GDP per capita are equal across time could not be rejected and, as a result, were imposed.
A number of different specifications of the ‘proximity’ variable were tested as shown in Table A1. The specification used in the estimates presented in the text is given by:
where distance is the airline distance between major cities. The variable measures the sum of world output discounted by distance – the square of the log of these figures is then taken to allow for non-linearities in the relationship.[42] Of the other measures, a number have been commonly used in the literature – for example Lawrence (1987) uses the log, and square of the log, of the fifth measure in the table. In addition, in order to allow for non-linearities in the relationship between distance and transport costs, the variables were entered in a number of different ways. It was consistently found that the specification of this variable had little impact on the results.
Formulae | How it entered the equation |
---|---|
![]() |
PROXj |
![]() |
ln(PROXj) |
![]() |
ln(PROXj), [ln(PROXj)]2 |
![]() |
ln(PROXj) |
![]() |
ln(PROXj), [ln(PROXj)]2, [ln(PROXj)]½ |
![]() |
PROXj, ln(PROXJ) |
Proximity variables on a regional basis were also constructed but were of limited success in estimation.
Where available, data were collected for the 66 countries set out in Table A2. Singapore was removed for the estimation because it was considered an outlier and was thought to influence the results. Senegal, Tanzania, Zimbabwe, Bangladesh, Malaysia, Yugoslavia, Iran, Honduras and Jamaica were excluded due to incomplete data. The model was then estimated for 56 countries. In the estimation, logs were taken of trade intensity, real GDP and real GDP per capita.
Group | Country | Major city | Group | Country | Major city |
---|---|---|---|---|---|
WH | Argentina | Buenos Aires | AF | Kenya | Nairobi |
IC | Australia | Sydney | AS | Korea | Seoul |
IC | Austria | Vienna | AS | Malaysia | Kuala Lumpur |
AS | Bangladesh | Dacca | E | Malta | Birkirkara |
WH | Barbados | Bridgetown | WH | Mexico | Mexico City |
IC | Belgium | Brussels | AF | Morocco | Casablanca |
WH | Bolivia | La Paz | IC | Netherlands | Amsterdam |
WH | Brazil | Sao Paulo | IC | New Zealand | Wellington |
AF | Cameroon | Douala | IC | Norway | Oslo |
IC | Canada | Ottawa | AS | Pakistan | Karachi |
WH | Chile | Santiago | WH | Panama | Panama |
WH | Colombia | Bogota | WH | Paraguay | Asuncion |
WH | Costa Rica | San Jose | WH | Peru | Lima |
E | Cyprus | Nicosia | AS | Philippines | Manila |
IC | Denmark | Copenhagen | IC | Portugal | Lisbon |
WH | Dominican Republic | Santo Domingo | AF | Senegal | Dakar |
WH | Ecuador | Quito | AS | Singapore | Singapore |
WH | El Salvador | San Salvador | AF | South Africa | Pretoria |
IC | Finland | Helsinki | IC | Spain | Madrid |
IC | France | Paris | AS | Sri Lanka | Colombo |
IC | Germany | Bonn | IC | Sweden | Stockholm |
OC | Greece | Athens | IC | Switzerland | Geneva |
WH | Guatemala | Guatemala | ME | Syrian Arab Republic | Damascus |
WH | Honduras | Tegucigalpa | AF | Tanzania | Dar es Salaam |
IC | Iceland | Reykjavik | AS | Thailand | Bangkok |
AS | India | New Delhi | AF | Tunisia | Tunis |
AS | Indonesia | Djakarta | E | Turkey | Ankara |
ME | Iran | Tehran | IC | United Kingdom | London |
IC | Ireland | Dublin | IC | United States | Chicago |
ME | Israel | Jerusalem | WH | Uruguay | Montevideo |
IC | Italy | Rome | WH | Venezuela | Caracas |
WH | Jamaica | Kingston | IC | Yugoslavia | Belgrade |
IC | Japan | Tokyo | AF | Zimbabwe | Harare |
The split into country groups is according to the IMF. IC denotes ‘industrial countries’, and ‘developing’ countries are split into: AF = Africa; AS = Asia; ME = Middle East; E = Europe; WH = Western Hemisphere.
Trade intensity is defined as (all in nominal
values), and is the variable ‘OPEN’ in the Penn World Tables
(5.5) (PWT).
Real GDP per capita in constant dollars (chain index) is the variable ‘RGDPCH’ in the PWT.
Real GDP is calculated by multiplying real GDP per capita by population which is the variable ‘POP’ in the PWT.
The distance data used to construct PROX were obtained from the Macintosh Map. The choice of major cities follows Frankel and Wei (1993). Where a country was not included in Frankel and Wei, the city with the largest population was used.
The variable measuring the degree of protection is defined as the ratio of customs duty (in domestic currency) to manufacturing imports (in domestic currency).
Data on customs duty in domestic currency were taken from the IMF Government Finance Statistics (various issues). Breaks in the custom data series may affect the 1975 observation for Denmark, Italy and the United Kingdom. The 1990 observation was unavailable for Argentina, Barbados, Canada, Chile, Colombia, Guatemala, New Zealand and South Africa and was replaced, where available, with the 1989 observation. For Chile and New Zealand the 1988 observation was used. In some cases customs data had to be adjusted for changes in the currency of denomination.
Data on manufactured imports in domestic currency used in the construction of the protection variable were taken from the UN Yearbook of International Trade Statistics, Volume 1 (various years). Manufactured imports are defined as BEC categories 4,5 and 6. Manufactured imports, rather than total imports, were used in the construction of the protection variable, given the perception that quantitative barriers were more common on non-manufactures (excluding textiles and apparel). However, the correlation coefficient between this measure and one based on total imports is above 0.9 in all years.
The use of a customs-based measure for protection is less than ideal. Dornbusch (1993) identifies a number of problems with such a measure. First, as elasticities of demand and supply vary over goods, an aggregate customs measure gives a poor indication of the marginal protective effect of a tariff. Second, it ignores the effects of protection on intermediate inputs and, third, it ignores non-tariff barriers. Prohibitive tariffs will also be understated using such a measure. Of particular concern is the possibility that as, over time, quantitative barriers are replaced by tariffs, these measures will imply rising protection.
Appendix B: Measures of Export Orientation and Import Penetration
When examining the openness of goods markets, it is common to look at the extent to which imports account for the supply of goods to the domestic market (their share in apparent consumption), and similarly, the proportion of domestic sales that is exported (see Industries Assistance Commission (IAC) (1985) and Gruen (1985)).
There are a number of problems with this sort of analysis. The first concerns the treatment of own-industry intermediate input in the construction of the domestic sales measure. This problem has two parts. First, these measures typically double count own intermediate input (OII). This can lead to a substantial under estimation of the level of orientation and penetration measures in sectors where own intermediate input usage is high – for example, in textiles, wood products, paper products, non-petroleum based chemicals, and basic metal products, own-industry intermediate input makes up over one fifth of ‘gross’ output (in an input-output sense) or sales. Further it double counts imported own intermediate inputs. Second, because the measures include OII when it is traded between establishments in an industry, but not when it is traded within the establishment, the level of the series is sensitive to the definition of ‘establishment’ used.
As a result of the first problem, estimates of the share of own intermediate input in gross output have been calculated from the 1989/90 input-output tables and used to adjust the level of turnover/sales used to calculate the penetration/orientation measures. The resulting change is most significant in those industries listed above where own intermediate input is a large proportion of gross output.
The second problem with the conventional analysis revolves around whether sales or turnover data are used, the former being available from a quarterly survey of business, and the latter from the Census of Manufacturing. Although the measure of sales is probably closer to the desired concept, the fact that turnover is a result of the Census and is thus likely to be more accurate means that it is used below. These data were also preferred in the IAC/Gruen series and so make the series constructed here more comparable to the earlier work. It should be noted that because sales is a narrower concept that turnover, measures created using the former data would lead to higher measures of import penetration and export orientation. In years where the Census was not undertaken, sales data from the Manufacturers Stocks and Sales release has been used to interpolate. The deflators used to construct constant price sales data have also been used to deflate the nominal turnover data (this is the process adopted by the ABS in the construction of constant price product data).
One final problem worthy of note relates to the ABS definition of activity undertaken in a business. Importantly, production undertaken by a business on commission for another company using that other company's own inputs (intermediate only) is not counted as production by that firm. However, the commission earned is included in turnover. The ABS believes that this could be a problem in the clothing and petroleum refining sectors.[43] The problem can be corrected for the petroleum refining industry because the major refiners changed the way they operated between 1988/89 and 1990/91 and began reporting the value of goods produced under commission for their parents as gross output. As a result, the ABS believes that turnover figures from 1990/91 accurately reflect the value of production by the industry. Nominal turnover data are then extrapolated backwards using volume measures of production (taken from ABARE) inflated using the APMI for petroleum products (this is the method used by the ABS to construct constant price value added data for the sector). However, it is impossible to make similar adjustments for the clothing data and so the level, if not the growth in, the series for this industry must be interpreted with caution.
In summary, import penetration has been calculated by taking f.o.b. total imports as a ratio to an estimate of the size of domestic sales. The latter has been calculated as turnover by domestic firms, less exports f.o.b., plus imports f.o.b., less an adjustment for own intermediate input to remove double counting of both own intermediate input produced at home and that which has been imported. Export orientation has been calculated as the ratio of exports f.o.b. to turnover of domestic firms, adjusted similarly for own intermediate input. All of the above uses volumes data. The adjustment for OII has been taken from the 1989/90 national accounts (which is the base year for constant price estimates). This has been calculated as advocated in Chapter 19 of the Australian National Accounts: Concepts Sources and Methods on Input-Output Tables (paragraph 19.34).[44] Using a table which allocates competing imports indirectly, the diagonal of the 1st quadrant (that containing own-industry intermediate input) has been used to obtain an adjustment factor for gross turnover. As a consistency check, the resulting series were then compared with those derived by IAC/Gruen – not surprisingly, given the adjustment, the constructed series is above that of the IAC/Gruen in every case but that of petroleum where a different turnover series has been used. The petroleum refining volumes series was compared to a series derived from ABARE data and was found to be very similar.[45]
Appendix C: Construction of Approximate Herfindahl Indices
The approximate Hirschman-Herfindahl indices (HHI) referred to in the text have been constructed using trade-adjusted concentration ratios by two methods described in Schmalensee (1977). The two methods (‘MIN’ and ‘MINL’ in Schmalensee's terminology) were ranked in the top 5 out of 12 plausible surrogates presented. The method MINL was the computationally least demanding of the top two surrogates and is the basis for the results presented in the text.[46]
The starting point for these measures is data on concentration ratios published by
the ABS. The concentration ratio corresponding to the share in some measure
of activity, A, of the firms in the k'th rank, is given by where Ak
is some measure of activity for the firms in the k'th rank (in the analysis
below, the measure is turnover or sales). In a closed economy context, the
ratio in terms of sales would take total sales of the four largest firms
as a proportion of the entire sales of the industry (note that the familiar
double counting of own industry intermediate input arises – this is
abstracted from below). When allowance is made for the open economy, the
relevant measures become
where X
represents exports, M imports, S sales. Unfortunately,
there is no data source on exports by size of firm constructed on the same
basis as these figures, and so it is usual to assume that exports of the
firms in the k'th rank are in proportion to their share of total
sales,
or
. X (Clark
1985). The ‘trade-adjusted’ (superscript ‘ta’)
concentration ratio for the k'th rank can then be written as
Obviously, if
larger firms are more likely to export, measures constructed on this basis
will overstate concentration in the industry. Another problem with the figures
is that it makes no distinction between total imports and those that are
‘competing’. In a number of industries it is believed that domestic
manufacturers are substantial importers of products and so not attributing
these to the firms themselves will understate their market power (offsetting
the bias in the export figures).
It is possible to then approximate the HHI using the trade-adjusted concentration
ratios. The simplest method, Schmalensee's MIN, is to take the average share for each class size (the Australian
data presents information on the market shares five ranks, each of four firms,
plus a remainder) given by where Nk
is the number of firms in the k'th rank, and then to construct
the approximate HHI as
where K
is the total number of ranks.
It is important to note that the figure MIN represents the minimum value the HHI
could take, given the concentration ratio data, because firms within ranks
are assumed to have exactly equal market shares. Importantly, if the degree
of equality in market share within ranks varies over time, then the magnitude
by which MIN understates the true HHI will also vary. The other measures
presented in Schmalensee (1977) involve making various assumptions about
how market share varies within ranks. Given that the largest firms have the
largest weights within the index, the methods which vary the share of the
top ranks of firms have the most effect. The method Schmalensee denoted MINL
makes the assumption that all firms in ranks, other than the top rank, have
shares equal to the average for that rank, however, the shares within the
top rank varied linearly with the smallest having the same share as the average
for the second rank. This proxy is calculated as which shows that
it always greater than the proxy MIN, and that the difference between the
two measures depends on the squared difference between the average shares
of the top two ranks.
Footnotes
The authors are especially grateful to Bill Mountford, Director of the Australian Manufacturing Council, for providing access to the results of the survey analysed in this paper. Anna Slomovic of RAND, and Philip Lowe of the RBA, provided helpful comments on an earlier draft; Scott Austin, Matthew Boge, Brian Brooke, Lynne Cockerell, Christine Groeger, Alex Heath, Eric Ralph, Mary Savva, and Geoff Shuetrim provided valuable assistance. However, the authors have sole responsibility for the views expressed. [*]
Estimates of the reduction in British protection following the repeal of the Corn Laws depend on the treatment of terms of trade changes. Data in Imlah (1958) on wheat prices prior to repeal imply a domestic price wedge before transport cost in excess of 50 per cent of the world price. However, as the elasticity of foreign supply was low, the effect of repeal in 1846 was to sharply increase world prices. McCloskey (1981) argues that the terms of trade effects were so great as to actually reduce British national income, the original tariff having been close to the ‘optimal tariff’. McCloskey's ‘best’ estimate of the extent of the tariff reductions is in the order of two-thirds. [1]
For a recent survey see Oulton and O'Mahony (1994). [2]
At least for industrial countries. Havrylyshyn (1990) notes that the proportion of growth explained by capital accumulation is generally much higher for developing countries. [3]
It is worth noting, however, that ‘… the ratio of exports or imports to national income overstates the relative importance of trade in domestic economic activity, increasingly so as the import content of exports rises. [Moreover], insofar as the proportion of traded goods destined for intermediate use varies between countries and over time, the ratio is an unreliable guide to either the ranking of countries by the relative importance of trade or to trends over time in the importance of international trade relative to total domestic output’ (Blackhurst, Marion and Tumlir 1977, p. 18). [4]
Note that these data are nominal, and thus vary from those presented in Figure 1. [5]
As a ratio to cumulated GDP, the respective figures were 1.9 and 1.1 per cent. The rise is despite regulatory changes which removed the bias against portfolio investment. [6]
Graham and Krugman (1993) argue that this is a better measure of the extent of foreign direct investment than statistics based on balance of payments data. For a more detailed discussion of trends in Australian FDI see the paper by Howe in this Volume. [7]
Using shares in annual FDI in the United States over the period 1976 to 1992 as the dependent variable, the regression line is given by:
where: DIST is distance of capital city from Washington, DC; PCAPGDP is per capita GDP at 1985 prices and current exchange rates; GDP is GDP in 1985 prices; R&D is Business Enterprise Outlays on R&D at 1985 prices; EXCHRATE is the percentage change in the US exchange rate over the previous five years; and t-statistics are in parentheses. Normalised by the mean error, the average gap between the actual and predicted value for Australia's share over the period to 1982 was −0.55; for the period from 1983 to 1992 it was +2.38.
[8]
Country j's RCA in industry i is given by where X
denotes exports.
[9]
Due to Lawrence (1984), the index measures structural change between two points in
time as where s
denotes share of, in this case, either value added or employment. A value
of zero implies complete stability in the economy's structure, whilst
a value of one implies a complete turnover.
[10]
This indicator was first presented in OECD (1987). An update is provided in Meyer-zu-Schlochtern (1994). The index is constructed by using the RAS adjustment procedure, commonly employed in updating input-output tables, to calculate ‘expected’ values of sector shares – that is, the values which would be observed if the sector share within each country evolved according to that sector's growth rate across all countries, corrected for the ratio of the economy-wide growth rate in that country, to the overall growth rate for the grouping of countries as a whole. The sum of the absolute values of the differences between the actual and the expected average annual growth rates for each country provides a measure of the extent of structural change in that country. [11]
The values of the index, calculated solely for manufacturing over the period from 1970 to 1989, are (setting Australia at 100), Sweden 196, UK 211, Canada 139, Japan 107, US 80. The index here is defined as: I = sum (absolute values [expected minus actual annual average growth rate of employment]) where the sum is taken over the following industry groups: Basic Metals, Food, TCF, Wood and Wood Products, Pulp and Paper, Chemicals, Non-Metallic Mineral Products, Fabricated Metal Products, Machinery and Equipment and Means of Transport. [12]
The decomposition arises by noting that manfacturing labour-productivity growth in
period 1 is approximately equal to the sum of the changes in individual industries
labour productivity levels weighted by their start-of-period share of total
hours worked (hsi,0) plus the sum of the changes in their
weights multiplied by their start-of-period labour-productivity level (pi,0)
relative to the aggregate (P0), or
[13]
That is, correlation of ‘environmental’ factors. Correlation of managerial talents may inhibit the monitoring process as managers free ride on each other's performance. See Vickers (1994) for an overview. [14]
Lee (1994) presents evidence that per capita income growth rates are positively related to the ratio of imported to domestically produced capital goods. See also Coe and Helpman (1993). [15]
There is considerable evidence on the impacts of internationalisation on price-cost margins. See, for example, Schmalensee (1989) and the studies referenced in Jacquemin and Sapir (1991) which are in the tradition of the older ‘gross margins’ literature, or the ‘new empirical industrial organisation’ studies of Levinsohn (1993) and Harrison (1994). [16]
Rodrik (1988) presents a model in which liberalisation, by reducing market share, reduces the incentive for the firm to make productivity improving investments. [17]
This is not the only factor at work. Reduced shirking may also arise in principal-agent models from the effect of intensified competition on the incentives of owners and managers to trade-off the incentive and insurance components of the contract between them, for example by altering the cost of slack. Thus, Horn, Lang and Lundgren (1991) develop a model which allows for international trade but in which all potential avenues for gains from trade, other than those associated with agency costs, are excluded. In this model, managers affect productivity as their effort is assumed to increase the productivity of labour – that is, to lead to a more efficient organisation of production. International trade then has an impact on the trade-off in the agency relation in two ways: it increases the perceived price elasticity of demand, which increases output and the incentives for owners to be tough; and it increases the demand for labour which increases real wages, and so adds further incentive to economise on labour by increased managerial effort. For models with similar mechanisms at work, see Horn, Lang and Lungdren (1990, 1994). In these models, competition can increase managerial effort without necessarily decreasing the degree to which the effort supplied is inefficient. [18]
Note that although many of the tau values seem small, this does not imply anything about the strength of the correlation. [19]
Import penetration measures at the industry level are likely to be too aggregated to adequately capture competitive conditions in particular product markets. These measures will overstate the degree of product market discipline exercised by trade flows when the imports in question are non-competing – be it because the incumbent domestic producers are the main importers (as is the case, for example, for paper) or because the imports are highly differentiated relative to domestic output. For example, Messerlin (1993) finds for France that domestic manufacturers account for 70 per cent of imports of home appliances, and for between 20 and 50 per cent of imports of textiles and apparel. Also see Utton and Morgan (1983). Equally, the measures will understate the disciplines trade imposes when the supply elasticity of imports at the margin is high – as may be the case in industries where competition occurs primarily on the basis of costs and where a few large retail chains account for a large share of purchases. [20]
Until March 1992, the survey was of Victorian manufacturers. ASIC 2-digit figures for this period have been reweighted at the 3-digit ASIC level using the 1989/90 input-output tables. [21]
On international trade and contestability, see Baumol and Lee (1991). [22]
We have relatively little faith in the MES estimates which were adapted from Mueller and Owen (1985), often augmented by arbitrary assumptions. However, the same results hold even if this variable is excluded from the analysis. [23]
The approach echoes that of Baily (1992). [24]
The overall level of industry demand, on the other hand, might be more stable, if cyclical positions internationally are not fully synchronised. Even so, given the impact of market widening on demand elasticities, the demand facing individual firms would probably become less predictable, all the more so once firms had lost the cushion of ‘made to measure’ protection. [25]
In a stochastic frontier production function study of technical efficiency in Australian manufacturing, Harris (1992) finds that tariffs increase the intra-industry dispersion in efficiency. This finding is confirmed for some other countries in Caves (1992a, 1992b). [26]
According to the Industry Commission (1993), outlays on the Passenger Motor Vehicle Export Facilitation Scheme were likely to amount to some $180 million in 1993–94, absorbing just over 20 per cent of outlays on specific export facilitation and assistance programs and 14 per cent of outlays on all export-related programs. [27]
Such a distinction is used in the ABS input-output tables, and by Industries Assistance Commission (1985) and Madge, Bennett and Robertson (1989). [28]
The Grubel-Lloyd index is defined as: I = 1 – [|X – M|]/[X + M]. [29]
It is worth noting that even in general equilibrium this result does not hold when competition is imperfect (Ventura and Cordella 1992). [30]
There may be a ‘40 per cent’ rule in this respect. Cross-sectional studies in areas as diverse as the explanation of wage structures, of educational outcomes and of the probability of bankruptcy typically explain no more than 40 per cent of the variance in the dependent variable. In other words, 60 per cent of the variance is within cell, almost regardless of the number of cells. The results presented here are usually well above and rarely below this benchmark. [31]
These findings echo those of Nickell (1993).33. It is, however, worth noting that rather similar studies for Japan, Taiwan and Korea, but which relied on questionnaires in which firms were asked to rank the intensity of competition they faced, did find a relation between the effort firms made in searching out external sources of information and the intensity of competition. See respectively Yoshitaka Okada, Interactive Learning and Techno-Governance Structures (manuscript) April 1994; Gee San, Study on Policy and International Priorities for Technology Development: The Case of Taiwan (manuscript) April 1994; Kee Young Kim, Policies and Institutions for Industrial and Technological Development: A Korea Study (manuscript) June 1994. [32]
It is, however, worth noting that rather similar studies for Japan, Taiwan and Korea, relied on questionnaires in which firms were asked to rank the intensity of competition they faced, did find a relation between the effort firms made in searching out external sources of information and the intensity of competition. See respectively Yoshitaka Okada, Interactive Learning and Techno-Governance Structures (manuscript) April 1994; Gee San, Study on Policy and International Priorities for Technology Development: The Case of Taiwan (manuscript) April 1994; Kee Young Kim, Policies and Institutions for Industrial and Technological Development: A Korea Study (manuscript) June 1994. [33]
For example, we find no link between competition and productivity growth, automation, most dimensions of time spent reviewing business performance, or likelihood of export-orientation. [34]
This is consistent with recent work on R&D which finds greater differences between those firms which carry out R&D, and those which do not, than between those which carry out some R&D, and some which carry out a great deal. It can be hypothesised that much like exporting, the R&D variable is picking up a greater interest and ability to learn about the outside world, and hence to adjust promptly to change. [35]
The general argument that export orientation is closely associated with productivity growth and some supporting evidence is set out in Balassa (1988). Important micro-level analyses are Dahlman, Ross-Larson and Westphal (1987) and Pack (1988). [36]
On East Asia, see World Bank (1993) and on Europe, see Mueller and Owen (1985) and the results (which in several respects parallel those reported here) in Zimmerman (1987). [37]
See, for example, Wade (1992) (on Taiwan), Amsden (1989) (on Korea), and Samuels (1994) (on Japan). The views expressed by these authors are controversial. See also essays in Krause and Kihwan (1991). [38]
Clearly, this gap may well be larger in a highly-dynamic economy than in one in which change is proceeding slowly. Nonetheless, there is no evidence to suggest that the larger gap observed in Australia arises from greater dynamism. Indeed, going by conventional indicators such as the FMS indicator in the ISDB, the rate of structural change in the Japanese and Taiwanese economies considerably exceeds that in Australia. [39]
The government's ‘industry plans’ each contain some mix of these measures, though they generally place less weight on strengthening market disciplines. The automotive industry plan, for example, appears to have resulted in substantial improvements in some indicators – for example, physical productivity, product quality and export orientation; but it also appears to have been associated with a fairly sharp rise in motor vehicle prices (Automotive Industry Authority 1993). It is arguable whether the ‘industry plan’ model could, or should be, used more broadly. It seems vulnerable to collusion and the problems which need to be tackled span so broad a range of industries that a more horizontal and industry-neutral approach seems preferable. [40]
Given that many of the worst performers report poor cash flow, greater competition is likely to substantially reduce their survival chances. [41]
See Balassa (1986) for a discussion of the relationship between distance and transport costs. [42]
The problem understates the level of sales and thus overstates the orientation/penetration measures. [43]
Note that this paragraph discusses how to construct a measure of ‘net’ domestic output, which involves subtracting the value of domestically sourced own intermediate input from gross output but leaving behind imported OII. For our purposes, to avoid double counting imported OII, this is removed as well. [44]
ABARE use a different distinction between refined and crude petroleum than does the ASIC. The ABARE data are from the Commodity Statistical Bulletin 1993, Table 269. [45]
Madge, Bennett and Robertson (1989) present results using Australian data for the MIN surrogate. [46]
References
Acs, Z.J. and D.B. Audretsch (1989), ‘Small-firm Entry in US Manufacturing’, Economica, 56(222), pp. 255–264.
Acs, Z.J. and D.B. Audretsch (1988), ‘Innovation in Large and Small Firms: An Empirical Analysis’, American Economic Review, 78(4), pp. 678–690.
Amsden, A. (1989), Asia's Next Giant: South Korea and Late Industrialization, Oxford University Press, New York.
Australian Manufacturing Council (1994), Leading the Way: A Study of Best Manufacturing Practice in Australia and New Zealand, Interim Report.
Automotive Industry Authority (1993), Report on the State of the Automotive Industry, AGPS, Canberra.
Bailey, S.D. (1992), ‘The Intraindustry Dispersion of Plant Productivity in the British Manufacturing Sector, 1963–79’, in R.E. Caves (ed.), Industrial Efficiency in Six Nations, MIT Press, Cambridge, pp. 329–384.
Balassa, B. (1986), ‘Japan's Trade Policies’, Weltwirtschaftliches Archiv, 122(4), pp. 745–790.
Balassa, B. (1988), ‘The Lessons of East Asian Development’, Economic Development and Cultural Change, Supplement, 36(3), pp. 273–290.
Baumol, W.J. and S.K. Lee (1991), ‘Contestable Markets, Trade and Development’, World Bank Research Observer, 6(1), pp. 1–17.
Blackhurst, R., N. Marion and J. Tumlir (1977), Trade Liberalisation, Protectionism and Interdependence, GATT, Geneva.
Caves, R.E. (1992a), ‘Determinants of Technical Efficiency in Australia’, in R.E. Caves (ed.), Industrial Efficiency in Six Nations, MIT Press, Cambridge, pp. 241–271.
Caves, R.E. (1992b), ‘Introduction and Summary’, in R.E. Caves (ed.), Industrial Efficiency in Six Nations, MIT Press, Cambridge, pp. 1–27.
Clark, R. (1985), Industrial Economics, Basil Blackwell, Oxford.
Coe, D.T. and E. Helpman (1993), ‘International R&D Spillovers’, NBER Working Paper No. 4444.
Cordella, T. (1993), Essays in International Trade and Strategic Behaviour, CIACO, Louvaine-la-Neuve.
Dahlman, C.J., B. Ross-Larson and L.E. Westphal (1987), ‘Managing Technological Development: Lessons from the Newly Industrializing Countries’, World Development, 15(6), pp. 759–775.
Dornbusch, R. (1993), Stabilisation, Debt, and Reform: Policy Analysis for Devloping Countries, Harvester Wheatsheaf, New York.
Frankel, J.A. and S.J. Wei (1993), ‘Is There a Currency Bloc in the Pacific?’ in A. Blundell-Wignall (ed.), The Exchange Rate, International Trade and the Balance of Payments, Reserve Bank of Australia, Sydney, pp. 275–307.
Gabszewicz, J.J. and P. Michel (1992), Oligopoly Equilibria in Exchange Economics, CORE Louvain.
Garnaut, R. (1991), ‘The End of Protection and the Beginnings of a Modern Industrial Economy: Australia in the 1990s’, Australian Quarterly, 63(1), pp. 15–23.
Graham, E.M. and P.R. Krugman (1993), ‘The Surge in Foreign Direct Investment in the 1980s’, in K.A. Froot (ed.), Foreign Direct Investment, NBER, UCP, Chicago, pp. 13–33.
Gruen, F. (1985), ‘How Bad is Australia's Economic Performance and Why?’, University of Western Australia Department of Economics Discussion Paper No. 85.14.
Harris, C.M. (1992), ‘Technical Efficiency in Australia: Phase 1’, in R.E. Caves (ed.), Industrial Efficiency in Six Nations, MIT Press, Cambridge, pp. 199–239.
Harrison, A.E. (1994), ‘Productivity, Imperfect Competition and Trade Reform: Theory and Evidence’, Journal of International Economics, 36(1/2), pp. 53–73.
Havrylyshyn, O. (1990), ‘Trade Policy and Productivity Gains in Developing Countries: A Survey of the Literature’, World Bank Research Observer, 5(1), pp. 1–24.
Hirschman, A.O. (1945), National Power and the Structure Of Foreign Trade, University of California Press, Berkeley.
Horn, H., H. Lang and S. Lundgren (1990), ‘“X”-Inefficiency and International Competition’, Institute for International Economic Studies Seminar Paper No. 480.
Horn, H., H. Lang and S. Lundgren (1991), ‘Managerial Effort Incentives, “X”-Inefficiency and International Trade’, Institute for International Economic Studies Seminar Paper No. 507.
Horn, H., H. Lang, and S. Lundgren (1994), ‘Competition, Long Run Contracts and Internal Inefficiencies in Firms’, European Economic Review, 38(2), pp. 213–33.
Imlah, A. (1958), Economic Events in the Pax Britannica, Harvard University Press, Cambridge, Massachusetts.
Industries Assistance Commission (1985), ‘Australian Trade Classified By Industry: 1968–69 to 1981–82: Working Paper’, IAC, Canberra.
Industry Commission (1993), Annual Report 1992–93, AGPS, Canberra.
Jacquemin, A. and A. Sapir (1991), ‘The Discipline of Imports in the European Market’, in J. de Melo and A. Sapir (eds), Trade Theory and Economic Reform: North, South, and East: Essays in Honor of Bela Balassa, Blackwell, Cambridge, pp. 154–162.
Krause, L.B. and K. Kihwan (eds) (1991), Liberalization in the Process of Economic Development, University of California Press, Berkeley.
Kuznets, S. (1959), Six Lectures on Economic Growth, The Free Press, Glencoe.
Lawrence, R.Z. (1984), Can America Compete?, Brookings Institution, Washington, DC.
Lawrence, R.Z. (1987), ‘Imports in Japan: Closed Markets or Minds?’, Brookings Papers on Economic Activity, 2, pp. 517–548.
Lee, J.W. (1994), ‘Capital Goods Imports and Long-Run Growth’, NBER Working Paper No. 4725.
Levinsohn, J. (1993), ‘Testing the Imports-as-Market-Discipline Hypothesis’, Journal of International Economics, 35(1/2), pp. 1–22.
Madge, A., R. Bennett and P. Robertson (1989), ‘Concentration in Australian Manufacturing, 1972–73 to 1986–87’, Bureau of Industry Economics Working Paper No. 57.
Maizels, A. (1963), Industrial Growth and World Trade, Cambridge University Press, Cambridge.
Martin, J.P. (1978), ‘X-inefficiency, Managerial Effort and Protection’, Economica, 45(179), pp. 273–286.
McCloskey, D.N. (1981), ‘Magnanimous Albion: Free Trade and British National Income, 1841–1881’, Enterprise and Trade in Victorian Britain: Essays in Historical Economics, George Allen and Unwin, London, pp. 155–173.
Messerlin, P.A. (1993), ‘The French Distribution Industry and the Openness of the French Economy’, OECD Economics and Statistics Department Working Paper No. 138.
Meyer-zu-Schlochtern, F.J.L. (1994), ‘An International Sectoral Database for Fourteen OECD Countries’, >OECD Economics Department Working Paper No. 145.
Mueller, J. and N. Owen (1985), Trade and Restructuring in German Industry: Lessons from Case Studies, DIW, Berlin.
Nickell, S.J. (1993), ‘Competition and Corporate Performance’, Oxford University Applied Economics Discussion Paper Series No. 155.
OECD (1987), Structural Adjustment and Economic Performance, OECD, Paris.
One Nation (1992), Statement by the Prime Minister, Prime Minister Keating, AGPS, Canberra.
Oulton, N. and M. O'Mahony (1994), ‘Productivity and Growth: A Study of British Industry 1954–1986’, National Institute of Economic and Social Research Occasional Paper No. 46.
Pack, H. (1988), ‘Learning and Productivity Change’, in The New Trade Theories and Industrialisation, World Institute for Development Economics Research.
Rodrik, D. (1988), ‘Closing the Technology Gap: Does Trade Liberalisation Really Help?’, NBER Working Paper No. 2654.
Samuels, R.J. (1994), Rich Nation, Strong Army: National Security and the Technological Transformation of Japan, Cornell University Press, New York.
Samuelson, P. (1939), ‘The Gains from International Trade’, Canadian Journal of Economics and Political Science, 5, pp. 195–205.
Scherer, F.M. et al. (1975), The Economics of Multi-Plant Operation: An International Comparisons Study, Harvard University Press, Cambridge, Massachusetts.
Schmalensee, R. (1977), ‘Using the H-Index of Concentration with Published Data’, Review of Economics and Statistics, 59(2), pp. 186–193.
Schmalensee, R. (1989), Inter-industry Studies of Structure Conduct and Performance' in R. Schmalensee and R. D. Willig (eds), Handbook of Industrial Organisation, Vol. 2, North-Holland, Amsterdam, pp. 951–1009.
Utton, M. and A. D. Morgan (1983), ‘Concentration and Foreign Trade’, National Institute of Economic and Social Research Occasional Paper No. 305.
Ventura, L. and T. Cordella (1992), ‘A Note on Redistribution and Gains from Trade’, Economics Letters, 39(4), pp. 449–453.
Vickers, J. (1994), Concepts of Competition, Clarendon Press, Oxford.
Wade, R. (1992), Governing the Market, Princeton University Press, Princeton, New Jersey.
World Bank (1993), The East Asian Miracle, Economic Growth and Public Policy, Oxford University Press, New York.
Zimmerman, K. (1987), ‘Trade and Dynamic Efficiency’, Kyklos, 40(1), pp. 73–87.